Lights Out Manufacturing ist ein Traum vieler produzierender Unternehmen. Davon auszugehen, dass die Fabrik der Zukunft völlig ohne Menschen auskommt, ist allerdings ein Trugschluss. [...]
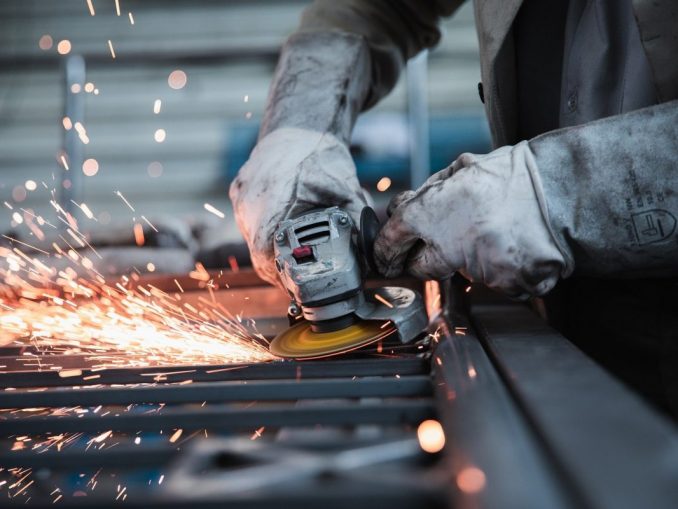
Als im Frühjahr 2020 die COVID-19-Pandemie die Welt auf den Kopf stellte, waren auch Industrieunternehmen und produzierende Firmen von weitreichenden Veränderungen betroffen. Dass die neue Situation viele Verantwortliche unvorbereitet traf, steht wohl außer Frage. Dabei waren nicht nur Konzepte wie Just-in-time-Produktion und enge Lieferketten von möglichen Ausfällen berührt. Branchen- und industrieübergreifend hat die Pandemie fast alle Unternehmen in ihrem Alltag beeinflusst.
Kein Wunder also, dass im Zuge der Pandemie der altbekannte Begriff Lights Out Manufacturing wieder in vieler Munde war. Das futuristische Konzept, in dem die Beleuchtung einer Fabrik entfällt, da zur Produktion keinerlei menschliches Einschreitennötig ist, kann vielen Verantwortlichen im ersten Augenblick interessant erscheinen. Davon auszugehen, dass eine vollautomatisierte Fabrik völlig ohne Menschen auskommt, ist allerdings ein gedanklicher Trugschluss. Für die Belegschaft einer Fabrik verändert die zunehmende Automatisierung trotzdem einiges im Arbeitsalltag – insbesondere hinsichtlich der Sicherheitsaspekte und der Aus- und Weiterbildung.
Lights Out Manufacturing – Wahr gewordene Utopie?
Die digitale Transformation und der Wandel hin zur Industrie 4.0 und zum Connected Enterprise lassen Lights Out Manufacturing zunehmend zur Realität werden. Mithilfe vernetzter Produktionsanlagen, die durch immense Datenmengen weitreichende Rückschlüsse auf die Produktion selbst und mögliche Schwierigkeiten bieten, lässt sich bereits heute eine weitgehend autonome Produktion realisieren. Autonome Förderwagen und die umfassenden Möglichkeiten, die diese Transportsysteme hin zur Losgröße 1 bieten, machen selbst komplexe Anlagen äußerst flexibel.
Die soft- und hardwareseitigen Errungenschaften der letzten Jahre haben hinsichtlich des Connected Enterprise dazu geführt, dass Anlagen weitgehend autonom funktionieren können und nur noch in Ausnahmefällen ein Eingreifen in die Produktion erforderlich ist. Für Anlagenbediener hat sich der Fokus ihrer Arbeit von der Anlage hin zum Leitstand verlagert. Ein nicht zu unterschätzender Vorteil, da so zu jedem Zeitpunkt die Sicherheit aller Mitarbeiter gewährleistet wird. Wer nicht in der Nähe von Fertigungsgeräten an einem HMI (Human-Machine Interface) arbeiten muss, läuft auch nicht Gefahr, durch bewegliche Maschinenelemente von der Anlage verletzt zu werden.
Die Möglichkeiten von Predictive und Prescriptive Maintenance bieten auch bei Instandhaltungsarbeiten weitreichende Flexibilität. Durch die Analyse von Produktionsdatenlassen sich Wartungs- und Instandhaltungsarbeiten problemlos planen und damit Kosten vermeiden. Die Analyse kann dabei granular bis auf einzelne Antriebe und Motoren heruntergebrochen werden,
Es lässt sich also konstatieren, dass eine moderne Anlage, die mit den Mitteln des Connected Enterprise arbeitet, heutzutage bereits weitgehend der Vision von Lights-Out Manufacturing entspricht. Betreiber von modernen und digitalisierten Anlagen hatten in der Folge auch in den Hochzeiten von Lockdown, Social-Distancing-Maßnahmen und starken Anforderungen an die Flexibilität innerhalb der Produktion einen großen Vorteil.
Lights Out – Menschen im Mittelpunkt
Entgegen der landläufigen Meinung, dass eine vollautomatisierte Fabrik gänzlich ohne Menschen auskommen würde und man daher auf Belüftung und Lichter ohne Probleme verzichten könne, führt der Weg der Digitalisierung innerhalb der Industrie vielmehr zu einer stärkeren Fokussierung auf menschliche Mitarbeiter. So geht etwa die Wissenschaftliche Gesellschaft für Produktionstechnik davon aus, dass die menschliche Belegschaft in Zukunft weiterhin eng mit den Anlagen und Maschinen arbeiten wird. So müssen auch selbstlernende Systeme in einem ersten Schritt angeleitet werden und selbst die weitgehend automatisierten Anlagen, die das Connected Enterprise ermöglicht, umfassen die Notwendigkeit von Instandhaltungs- und Wartungsarbeiten und müssen im Betrieb überwacht werden.
Damit alle diese Aspekte durch Angestellte erledigt und die Produktion weiterlaufen kann, ist die Aus- und Weiterbildung von Mitarbeitern ein Aspekt, der schon jetzt von Verantwortlichen in die richtige Richtung getrieben werden muss. Glücklicherweise sind auch hier moderne Technologien Dreh- und Angelpunkt einer umfangreichen Digitalisierung von bislang eher analogen Fortbildungsszenarien.
So hat beispielsweise die Pandemie mehr denn je gezeigt, dass der dringend benötigte Wissenstransfer, der durch den Fachkräftemangel konstant verschlimmert wird, auch ohne direkte menschliche Interaktion und damit ortsübergreifend geschehen kann. Neben dem zentralen Aspekt der Weiterbildung kann aber auch die Instandhaltung mithilfe der richtigen Technologien über Fernwartung erledigt werden, wie aktuelle Beispiele zeigen.
Fabrik der Zukunft – AR und VR als Ergänzung
Wie gut moderne Technologien sich zur Fernwartung und zum Wissenstransfer eignen, lässt sich anhand der Arbeit der SN Maschinenbau GmbH erkennen. Das Unternehmen ist spezialisiert auf Verpackungsmaschinenlösungen für die Getränke- und Lebensmittelindustrie sowie andere Branchen. Da sich die Anlagen und Maschinen des Unternehmens in Produktionsstätten weltweit befinden, hat man sich schon früh dazu entschlossen, auf moderne Mittel zur Fernwartung zu setzen.
Mithilfe eine kollaborativen Lösung können Fachkräfte von SN Maschinenbau in direkten Kontakt mit den Kunden treten, über Smart Glasses zielgerichtete Anweisungen zur genauen Fehlerbehebung geben und Schritt-für-Schritt-Anleitungen zur Instandhaltung mit dem jeweiligen Kunden teilen. Der Wissenstransfer ist auf diese Weise weltweit und unabhängig von Beschränkungen wie Social Distancing oder Quarantänemaßnahmen möglich. Darüber hinaus können Probleme, die bei vollautomatisierten Systemen auftreten können, immer einem jeweiligen Experten zugewiesen werden, ohne dass dieser tatsächlich vor Ort sein muss.
Moderne Werkzeuge wie bei SN Maschinenbau im Einsatz sind dementsprechend als Ergänzung zu den Möglichkeiten der weitgehenden Vernetzung und Automatisierung auf Anlagen- und Maschinenebene zu verstehen. Während die Produktion immer autonomer wird, erhalten menschliche Mitarbeiter an dieser Stelle die Infrastruktur bereitgestellt, die sie benötigen, um sich vollumfängliches Wissen über die Maschine aneignen zu können.
Mithilfe von AR und VR lassen sich Schulungen und Hintergrundinformationen zur Anlage so aufbereiten, dass Fachwissen aus der aktuellen Belegschaft für künftige Mitarbeiter gespeichert und jederzeit zugänglich gemacht werden kann. Auf diese Weise kann im Fall eines notwendigen Eingriffs oder nicht maschinell durchführbarer Umbaumaßnahmen ein weitreichender Wissensvorsprung erreicht werden. Dieser kann heutzutage bereits den notwendigen Unterschied machen und die Basis für eine zukunftsfähige Anlage darstellen.
Lights Out Manufacturing – der Utopie längst entwachsen
Lights Out Manufacturing geht mittlerweile über ein theoretisches Konzept oder gar eine Utopie hinaus. Ganz im Gegenteil: Bereits heute lässt sich mit den Mitteln des Connected Enterprise eine Produktionsumgebung errichten, die auch bei ausgeschalteter Beleuchtung ihren Zweck erfüllen kann. Dass menschliche Mitarbeiter in Zukunft aber aus der Produktion verschwinden werden, ist ein weitreichender Trugschluss, dem Verantwortliche nicht aufsitzen sollten.
Es ist davon auszugehen, dass Angestellte künftig noch zentraler für die Produktion werden. Deswegen müssen Unternehmen erkennen, wie unabdingbar es ist, ihren Mitarbeitern die Werkzeuge an die Hand zu geben, mit denen sie sich Fachwissen und umfangreiche Fähigkeiten aneignen können. Schlussendlich muss nämlich auch bei Lights Out Manufacturing von Zeit zu Zeit das Licht angeknipst werden.
*Gunther Sälzler ist Field Business Leader Architecture & Software bei Rockwell Automation.
Be the first to comment