Über einen Digital Thread lassen sich Daten aus diversen Quellen zusammenfügen und so komplette Werke digital abbilden. Richtig angegangen, bieten sie für Unternehmen und Mitarbeiter einen echten Mehrwert. [...]
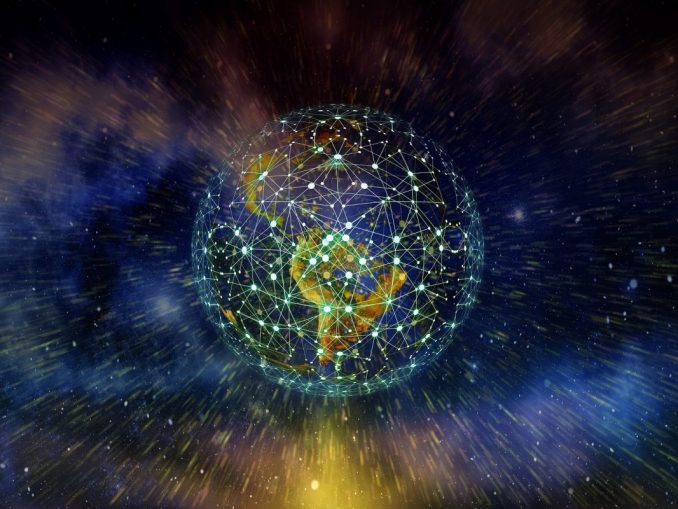
Ganz gleich ob Produktentwickler, Ingenieure oder Servicetechniker: Sie alle sind auf aus diversen Bereichen angewiesen, um ihre Aufgaben verrichten zu können. Dabei kommen diese oft nicht nur aus der eigenen Anlage oder der Fabrik, sondern auch von Partnern oder Zulieferern. Diese Daten miteinander zu verknüpfen und an relevanten Stellen zugänglich zu machen, ist die Aufgabe des Digital Thread. Wie durch einen roten Faden werden mit ihm Daten vernetzt.
Das Besondere: Es gibt nicht nur eine Digital-Thread-Technologie – stattdessen werden aus unterschiedlichen Quellen ein Mix diverser zusammengefügt und verwebt – selbst wenn sie aus verschiedenen IT-Systemen stammen. So ermöglichen Digital Threads, die richtigen Daten zur richtigen Zeit zu liefern.
Digital Thread verarbeitet verschiedene Daten
Die Daten, die durch einen Digital Thread miteinander verknüpft werden, lassen sich grob in zwei Gruppen aufteilen: Da sind zum einen „digitale Definitionen“ und zum anderen „physikalische Erfahrungen“. Zur ersten Gruppe gehören zum Beispiel Daten aus PLM-Systemen, die wiederum CAD-Daten oder Informationen aus ERP/CRM-Systemen abrufen.
Die physikalischen Daten hingegen umfassen Informationen zu einzelnen Maschinen oder produzierten Produkten, seien es Stückzahlen, bearbeitete Aufträge, Wartungen und auch die Reparaturhistorie. Diese Daten werden beispielsweise über Sensoren erfasst und auf IIoT-Plattformen (Industrial Internet of Things) aggregiert und weiterverarbeitet.
Der Digital Thread bringt all diese Daten zusammen und muss, um wirklich effektiv zu sein, im nächsten Schritt die Daten so anzeigen, dass der Anwender eine informierte Entscheidung treffen kann. Dabei gilt es Einiges zu beachten, um am Ende einen gut funktionierenden und auf die eigenen Anforderungen abgestimmten Digital Thread implementieren zu können.
Eine breite Palette von Technologien kommt zum Einsatz
Bei der Implementierung eines Digital Thread treten drei Technologien besonders in den Vordergrund: PLM, IIoT und AR. Diese Technogien stechen besonders hervor, da sie gut geeignet sind, um Prozessoptimierungen durchzuführen, Mitarbeiter effizient anzulernen und Produkte zu differenzieren.
Über PLM-Systeme lassen sich Daten aus uneinheitlichen Quellen miteinander verbinden und den vollständigen Lebenszyklus abbilden. So können wichtige Informationen bereitgestellt werden, die zum Beispiel ein Serviceteam für eine Reparatur benötigt und neue Generationen von Produkten lassen sich mithilfe der Daten optimieren. Verknüpft mit einem IIoT-System, beschleunigen PLM-Systeme Produktentwicklung und -Einführung, Abteilungen können miteinander vernetzt werden und auf vereinheitlichte Datengrundlagen zurückgreifen.
IIoT-Systeme zeichnen sich durch ihre Leistungsstärke in der und Orchestrierung von Informationen aus. Mit ihnen können komplette Anlagen und Systeme vernetzt werden, Daten aus allen relevanten Quellen gezogen und auch externe IT-Daten einbezogen werden. Darüber hinaus kontextualisiert die IIoT-Anwendung die Daten und kann so die jeweils relevanten und aktuellen Daten übersichtlich aufbereitet zur Verfügung stellen. Die Daten lassen sich zudem analysieren, um einen genaueren Einblick in die Prozesse einer Anlage zu gewinnen. Somit kann die Gesamteffektivität (Overall Equipment Efficiency, OEE) einer Anlage verbessert und Kapazitäten optimiert werden.
AR unterstützt alle Mitarbeiter einer Fabrik dabei, ihren Arbeitsalltag intuitiver und leichter zu gestalten. Durch den Einsatz von Augmented Reality können Techniker zum Beispiel leichter Reparaturen und Wartungen an Maschinen durchführen. AR führt sie durch alle relevanten Schritte oder ermöglicht es, mit einem Experten per Videochat die Reparatur durchzuführen. Auch ungeschulte Mitarbeiter können durch AR-Anleitungen schnell in den Job finden und direkt produktiv in den Arbeitsalltag einsteigen.
Damit auch alle Daten aus manuellen Vorgängen erfasst und im Digital Thread abgebildet werden, kann ein Managementsystem für Entwicklungsstücklisten und eine Plattformstruktur in die Planung einbezogen werden. So wird verhindert, dass wichtige Informationen fehlen und Fehler entstehen.
Erste Schritte planen
Ebenso wie es nicht nur eine für Digital Threads gibt, gibt es auch nicht den einen Anwendungsfall. Entsprechend muss der Einsatz strukturiert geplant werden, damit ein möglichst hoher Mehrwert generiert werden kann. Als erster Schritt steht also die Identifikation der Anwendungsfälle im eigenen Unternehmen und die Frage, welches Ziel mit dem Digital Thread erreicht werden soll. Es muss ermittelt werden, an welchen Stellen die Mitarbeiter Daten über diverse Abteilungen oder Unternehmen hinweg benötigen.
Für den Start kann hier ein Teil der Daten ausreichend sein, die restlichen Daten können an anderer Stelle für die spätere Verwendung eingelagert werden. Dieser Ansatz mag für viele ungewöhnlich erscheinen, schließlich wird oft davon ausgegangen, dass es umso besser ist, je mehr Daten verarbeitet werden. Im Endeffekt steht so aber häufig ein zu komplexes , das letzten Endes in einer Schublade verschwindet, anstatt im Unternehmen den Mitarbeitern zur Verfügung zu stehen.
Keep it simple
Zu hohe Komplexität kann also das Aus für ein Digital-Thread-Projekt bedeuten. Durch die Nutzung lediglich eines Teils der Daten wird diese Problematik vermieden. Dabei sollten sich Unternehmen aber nicht zu sehr einschränken und bereits bei der Planung für künftige Anwendungsfälle vorsorgen, bei denen dann gegebenenfalls andere Daten benötigt werden, als beim ersten Aufschlag. Außerdem muss bedacht werden, dass auch die bereits geplanten Anwendungsfälle nicht in Stein gemeißelt sind, sondern eher ein übergeordnetes Thema für diverse individuelle Situationen darstellen. Schließlich ist nicht jede Fehlermeldung, nicht jede Wartung und nicht jeder Reparaturprozess identisch. Somit gleicht die Planung einer Gratwanderung zwischen zu komplexen Gebilden und einer zu stark vereinfachten Datenstruktur.
Digitalisierung zu Ende gedacht
Wie konkret die Verbindung und Verarbeitung der Daten aussehen kann, zeigen erfolgreiche Beispiele der Digital-Thread-Technologie wie die Next e.GO Mobile SE. Das Unternehmen gilt als Pionier im Bereich Elektromobilität und hat die eigenen Produktionshallen in Aachen komplett digitalisiert. Hier kann beispielsweise ein Qualitätsprüfer an einem gerade erst produzierten Modell die Seriennummer scannen und schon erhält er Einblick in den kompletten Produktionsprozess: Welche Konfiguration wurde vorgegeben, wo gab es Mängel und welche Hinweise oder Beobachtungen müssen an die verantwortlichen Teams zurückgespielt werden? Er kann ganz einfach ein Foto machen, die jeweiligen Anmerkungen markieren und sie auch in der digitalen Fahrzeugakte abspeichern.
Und die Next e.Go SE ist nur eines von vielen Digital-Thread-Beispielen, bedenkt man die vielfältigen Anwendungsfälle. Der digital rote Faden zieht sich zum Beispiel Konstruktionsdaten aus der CAD-Software und parallel Stückzahlen aus dem PLM-System. Auch kundenrelevante Daten aus dem CRM-System können einbezogen werden. Informationen zur Wartungshistorie einer Maschine und Reparaturanweisungen können mittels Augmented Reality eingeblendet werden und die Daten aus dem IIoT-System werden zeitgleich in die Berechnungen einbezogen. All das ermöglicht den Mitarbeitern schneller und effizienter zu arbeiten und sich auf die wichtigen Aufgaben zu konzentrieren, da Informationen nicht erst langwierig gesucht werden müssen.
Digitalisierung in Theorie und Praxis
Bei vielen Unternehmen gibt es allerdings ein grundlegendes Problem auf dem Weg zur vollständig digitalisierten und vernetzten Fabrik: Die gewachsenen Strukturen lassen es schlicht nicht zu. Altsysteme, die schwer miteinander zu vernetzen sind, eine nicht vorhandene Digitalarchitektur oder sogar rechtliche Hindernisse: In der Theorie klingt die Digitalisierung oft wesentlich einfacher, als sie sich praktisch umsetzen lässt. Deshalb müssen auch beim Einsatz des Digital Thread erste Schritte sorgsam geplant werden.
*Markus Hannen ist Vice President Go-to-Market bei PTC.
Be the first to comment