Im Rahmen von Industrie 4.0 und damit komplexer werdender Systeme sind die Anforderungen an die Sicherheit nicht nur im Bezug auf Security, sondern auch im (Machinery) Safety-Bereich mit entsprechender Sorgfalt zu betrachten. [...]
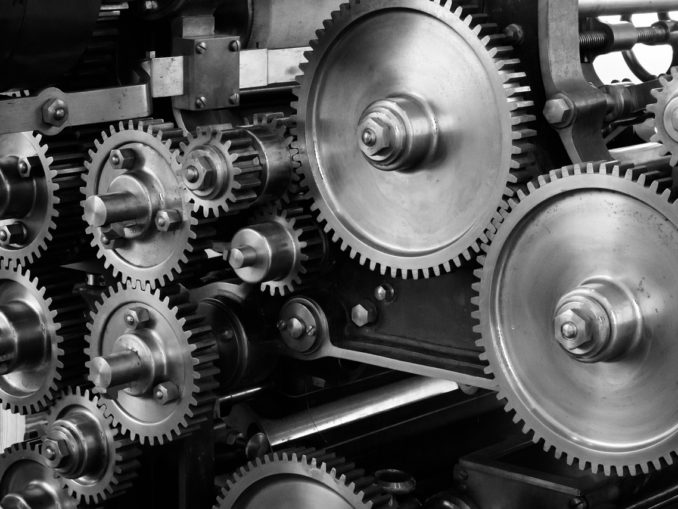
Die, aktuell viel diskutierte, DSGVO fordert das Erstellen eines Datenverarbeitungsverzeichnisses. Damit soll sich jeder Betrieb, schon vor entstandenem Schaden, Gedanken über möglichen Datenverlust und die Konsequenzen machen. Der wichtige Punkt dabei ist, dass alle möglichen Schwachstellen dabei aufgedeckt und entsprechende Maßnahmen dagegen getroffen werden.
Ähnlich wie bei der DSGVO fordert die, in Österreich als Maschinensicherheitsverordnung umgesetzte, europäische Maschinenrichtlinie 2006/42/EG schon seit vielen Jahren von Maschinenherstellern, eine Risikobeurteilung durchzuführen. Damit soll sichergestellt werden, dass alle notwendigen risikomindernden Maßnahmen vor dem Inverkehrbringen der jeweiligen Maschine umgesetzt werden.
Risikobeurteilung
Die, nach der Maschinenrichtlinie, harmonisierte Norm EN ISO 12100 gibt eine strukturierte Vorgabe, wie eine Risikobeurteilung inhaltlich zu gestalten ist.
Bei der Festlegung der Grenzen der Maschine gilt es, neben räumlichen und zeitlichen Grenzen unter anderem die bestimmungsgemäße Verwendung zu definieren. Diese wird auch in der Betriebsanleitung beschrieben. Damit soll eine mögliche Fehlanwendung und daraus resultierende Gefährdungen verhindert werden. Dem Betreiber der Maschine soll damit eine eindeutige Anleitung gegeben werden, um die Maschine sicher betreiben zu können.
Der inhaltlich größte Teil der Risikobeurteilung ist die Identifizierung der Gefährdungen. In diesem Schritt sind nicht nur mechanische und elektrische, sondern auch alle weiteren Gefährdungen aufzudecken. Ein häufiger Mangel zeigt sich in diesem Punkt darin, dass nur der Normalzustand der Maschine betrachtet wird, d.h. Automatikbetrieb ohne Störungen. Für diesen Zustand gibt es dann als mögliche risikomindernde Maßnahmen einen Schutzzaun und eine Schutztür. So weit, so gut. Doch wenn man sich die EN ISO 12100 zu Gemüte führt, wird schnell klar, dass dies bei weitem noch nicht alles ist. Vielmehr sind zusätzlich alle anderen Betriebsarten, z.B. Manuell, alle Maschinenzustände, z.B. Störung und alle Lebensphasen der Maschine, z.B. die Wartung und die, in diesen Situationen entstehenden Gefährdungen, ebenfalls zu identifizieren.
Häufig erkennt man bei genauer Betrachtung von Gefährdungen, die während einer Störung auftreten, dass es bei bestehenden Maschinen keine Möglichkeit gibt, die Störung gefahrlos zu beheben. Diese Störung wurde in einem solchen Fall in der Risikobeurteilung nicht oder nur unzureichend betrachtet. Dem findigen Bedienpersonal bleibt dann häufig nur noch die rechtswidrige Manipulation der Maschine. Würde die Risikobeurteilung korrekt durchgeführt, so hätte man z.B. einen Betriebsartenwahlschalter vorsehen können, der eine Betriebsart für die sichere Störungsbehebung mit entsprechenden Sicherheitsfunktionen vorsieht.
Risikominderung
Sind sämtliche Gefährdungen identifiziert, so sind im Normalfall risikomindernde Maßnahmen zu setzen. Ein häufiger Fehler, der dabei passiert ist, dass die Risikobeurteilung zu einem sehr späten Zeitpunkt durchgeführt wird, d.h. die Maschine wird zunächst fertig gebaut und erst in einem nächsten Schritt überlegt man sich, wie die Maschine sicher zu gestalten ist.
Der für den Hersteller unerfreulichste Punkt dabei ist, dass eine solche Vorgehensweise die Kosten zu einem sehr späten Projektzeitpunkt in die Höhe treibt, weil es dann meist nicht mehr möglich ist, konstruktive Änderungen durchzuführen. Stattdessen werden zusätzliche technische Maßnahmen realisiert, die teils ungünstig, teils einfach nur kostspielig sind.
Das zweite Problem bei der verspäteten Risikobeurteilung ist der Widerspruch zur EN ISO 12100. Die Norm gibt nämlich sehr klar und eindeutig die Vorgehensweise bei der Risikominderung vor. Hier ist das 3-Stufen-Verfahren anzuwenden, bei dem der erste Schritt immer die inhärent sichere Konstruktion ist. Nur die Gefährdungen, die konstruktiv nicht zu mindern sind, dürfen durch technische und ergänzende Schutzmaßnahmen gesichert werden. Der dritte und letzte Schritt macht gleichfalls deutlich, dass das alleinige Anbringen von Warnschildern noch lange keine CE-konforme Maschine macht.
* Sascha Steinkrauß ist Geschäftsführer von 4S – Sascha Steinkrauß Safety Services e.U. und unterstützt Maschinenhersteller und Maschinenbetreiber bei der Risikobeurteilung gemäß MSV2010, oder der Gefahrenanalyse gemäß ASchG.
Be the first to comment