KVP heißt Verbesserung. Wir zeigen, wie KVP konsequent umgesetzt die Wettbewerbsfähigkeit von Unternehmen entscheidend steigern kann. [...]
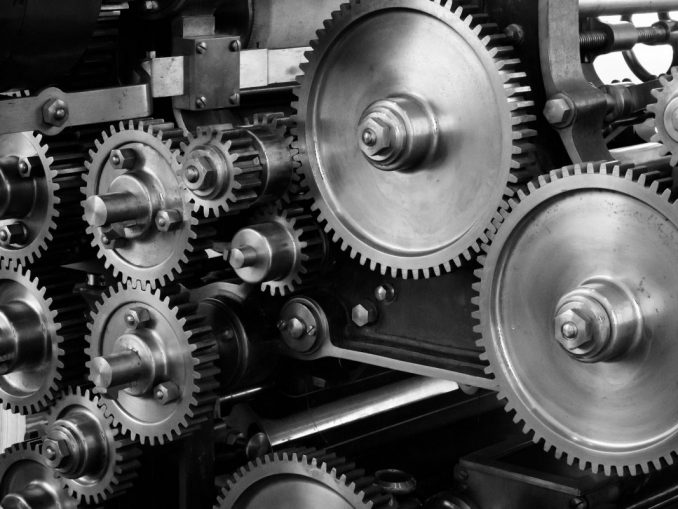
Von einem Release im Monat auf 250 Releases pro Woche, wie schafft man das? Wie bekommt man ausreichend Spielraum für Innovation und Experimente, wenn die Anforderungen des Tagesgeschäfts immer wieder vorrangig bedient werden müssen? Wie wird die IT vom Cost Center zum Innovationsbeschleuniger? Wie bindet man Mitarbeiter in die Wertschöpfung ein und nutzt ihr gesamtes Potenzial? Die Fragen sind geläufig, aber kontinuierliche Verbesserung haben Sie sicher selten als Antwort gehört.
KVP – eine Definition
Ein kontinuierlicher Verbesserungsprozess (KVP, auch: Kaizen) bedeutet, dass ständig, systematisch und in kleinen Schritten an der Optimierung aller Abläufe eines Unternehmens gearbeitet wird. Das Prinzip wird in weiten Teilen der Fertigung und Industrie angewandt; prominentestes Beispiel ist Toyota, wo Kaizen eine der beiden tragenden Säulen des Toyota Production System ist.
KVP entwickelt ganze Organisationen weiter
Die Wirkung kontinuierlicher Verbesserung geht weit über die einzelne kleine Verbesserung hinaus. Nach einer Meldung von Leanblog wurden 2019 an den japanischen Toyota-Standorten 430.000 Vorschäge im Jahr umgesetzt, das entspricht durchschnittlich 6,3 pro Mitarbeiter und Jahr. Der kumulative Effekt von Tausenden Verbesserungen führt bei Toyota zu sehr effektiven Abläufen, hoher Qualität, zufriedenen Mitarbeitern und schließlich auch zu geringen Kosten. Die Prinzipien des Toyota-Produktionssystems werden seit den 1980er Jahren erforscht und als „Lean Production“ beziehungsweise „Lean Thinking“ zusammengefasst.
Einige Elemente des Lean Thinking wurden in den letzten Jahren auf weitere Branchen wie das Gesundheitswesen und in die IT übertragen. Gerade im IT-Bereich werden mit (Software-)Kanban und der DevOps-Bewegung Prinzipien wie der Fokus auf Qualität, begrenztes WIP (Work In Process) und kurze Durchlaufzeiten übernommen. Auch die andere Säule des Toyota Production System „Respect for People“ findet Parallelen in autonomen Teams und New Work sowie agiler Führung.
Im Unterschied zu Lean in der Fertigung fokussiert man sich hier auf das Projektgeschäft und die moderne Software-lastige Produktentwicklung, wo höhere Unsicherheit herrscht und mehr Flexibilität und Reaktionsfähigkeit von Organisationen gefordert werden. In diesem Sinne ist KVP ein ganzheitlicher, systemischer Ansatz, der Werkzeuge und Methoden sowie Haltung und Wertesystem gleichermaßen berücksichtigt.
Kontinuierliche Verbesserung ist ein Instrument zur Weiterentwicklung der gesamten Organisation, vor allem der Menschen, die in ihr arbeiten. Wenn Kaizen konsequent und systematisch angewandt wird, kann es auch wesentlich dazu beitragen.
- die Beziehung zwischen Management und Teams zu stärken, indem Führungskräfte hands-on mithelfen, ein konkretes Problem zu lösen.
- Führungsnachwuchs zu identifizieren, denn um Verbesserungen umzusetzen braucht es nicht nur fachliche sondern auch soziale Kompetenzen.
- Mitarbeiter zu involvieren, denn wer Prozesse verändern kann, macht sie sich zu eigen und erlebt sie nicht als „von oben“ diktiert.
- Autonomie zu fördern, weil alle ermächtigt und befähigt werden, die eigenen Probleme zu lösen.
- Fluktuation zu verringern, weil die Mitarbeitenden zufriedener sind und hier mehr bewegen können als bei der Konkurrenz.
- Leute fortzubilden, indem sie mehr über die Zusammenhänge im Unternehmen lernen.
- Teamwork zu fördern, insbesondere wenn abteilungsübergreifende Gruppen gemeinsam an einer Verbesserung arbeiten.
- Unternehmenskultur zu formen durch den Austausch und durch gemeinsames Verständnis über Unternehmensziele.
Diese Effekte sind sehr erwünscht – nur leider sind die detaillierten Verbesserungsschritte unterhalb der Flughöhe, für die sich das Management normalerweise zuständig fühlt.
KVP dauerhaft etablieren – einige Beispiele
Der Schweizer Klebebandhersteller Siga reserviert laut einem Bericht von brand eins aus dem Jahr 2015 jahrelang jeden zehnten Arbeitstag für das Nachdenken über Arbeitsabläufe und Fehler und generierte so 20.000 Verbesserungsideen im Jahr, von denen zwei Drittel auch umgesetzt werden. Jeden zweiten Freitag ruht die Arbeit in Büros, und die Produktionsanlagen stehen still. Die Teams probieren an diesen Tagen Verbesserungen aus und setzen sie wenn möglich sofort um. Siga hatte damals 400 Mitarbeiter, das macht durchschnittlich 50 Ideen pro Mitarbeiter und Jahr. Die Verbesserungen können klein sein, es wird im Team entschieden, was umzusetzen ist. Die Geschäftsführung von Siga meint, dass man ohne die vielen Verbesserungen schon lange nicht mehr im Hochlohnland Schweiz produzieren könnte.
Die amerikanische Firma FastCap produziert Werkzeuge und Zubehör für Möbelhersteller und Baufirmen. Vor dem Beginn der eigentlichen Arbeit hat jeder Mitarbeiter jeden Tag eine Stunde reservierte Zeit, um aufzuräumen und kleine Verbesserungen sofort umzusetzen. Das Konzept heißt „2 Second Lean“, wobei sich „2 Second“ auf das einzige Kriterium für Verbesserungen bezieht: sie müssen mindestens 2 Sekunden Zeit sparen. Es ist also eigentlich eine clevere nicht-Hürde, die verhindert, dass man Verbesserungen zu Tode analysiert statt sie zu machen. Im Laufe der Zeit sind aus kleinen (und nicht ganz so kleinen) Verbesserungen dramatische Produktivitätsgewinne entstanden, parallel dazu wurde die Arbeit einfacher und sicherer.
Der amerikanische Krankenhausbetreiber Thedacare konnte die Fehlerquote bei Blutentnahmen innerhalb von zwei Jahren um 60 Prozent senken, durch wiederholte Verbesserung aller relevanten Abläufe in kleinen Schritten. Mit demselben Vorgehen wurden die Fehler in Laborwerten um 73 Prozent gesenkt. Durch eine Fülle von einzelnen Kaizen-Maßnahmen, die durch Mitarbeitende selbst initiiert und durchgeführt werden, konnte beispielsweise die Produktivität im Laborbereich innerhalb von vier Jahren um 24 Prozent gesteigert werden.
Kontinuierliche Verbesserung für IT
Ein wesentliches Ziel für die Verbesserung im Projektgeschäft und in der Produktentwicklung ist es, die Zeit von der Idee bis zur Umsetzung immer weiter zu verringern. Dies entspricht der Anforderung aus der Fertigung: den Zeitraum von der Bestellung bis zum Zahlungseingang immer weiter zu verkürzen. Daraus ergeben sich untergeordnete Teilziele, wie etwa Steigerung der Qualität oder der Häufigkeit von Releases (bis hin zum Continuous Deployment).
Ansatzpunkte für kontinuierliche Verbesserung finden sich zuhauf:
- Overhead für Releases,
- Monitoring,
- Performance,
- Regressionstests,
- die Bereitstellung von Test- und Entwicklungsumgebungen uvm.
In der eigentlichen Softwareentwicklung wird häufig das Refactoring in kleinen Schritten als kontinuierliche Verbesserung der Code-Qualität praktiziert. Eine ganzheitliche Betrachtung bezieht auch indirekte Faktoren ein: Wie kann man Missverständnisse in der Kommunikation mit den Stakeholern vermeiden? Wie lassen sich Meetings effektiver machen? Was kann man beim Onboarding von neuen Mitarbeitern besser machen?
In diesen Bereichen sind große Vorhaben oder Investitionen denkbar, die von heute auf morgen ein Problem ein für alle Mal lösen. Im Gegensatz dazu besteht Kaizen aus vielen Schritten, von denen jeder einzelne klein, schnell und risikoarm ist.
Starten ist einfach
Wie so vieles braucht auch KVP eine gewisse Anlaufunterstützung und Engagement, bis sich sichtbare Erfolge einstellen und eine Eigendynamik entstehen kann. So können Sie beginnen:
1. Identifizieren Sie ein Ziel. Das Ziel sollte möglichst konkret, ambitioniert und messbar sein, etwa den Overhead für ein Release von sieben Tagen auf zwei Stunden zu senken. Oder den Anteil von „Fire Fighting“ (ungeplante Arbeit) von 60 Prozent auf 10 Prozent zu verringern. Wählen Sie ein Gebiet, auf dem Verbesserungen einen großen Effekt haben können. Wenn Sie sich auf ein Ziel beschränken, können sich viele kleinen Verbesserungen relativ schnell zu einem sichtbaren Gesamtergebnis summieren.
2. Beginnen Sie mit einem konkreten Problem. Das Problem darf klein und unspektakulär sein, gern aus der Rubrik: „Ja, das wäre sinnvoll, aber wir kommen nie dazu“. Wenn z.B. bei einem Release immer ein Tag für die Aktualisierung der Testumgebung aufgewandt wird, kann man sich vornehmen, ein paar der nötigen Schritte zu automatisieren, um zukünftig vielleicht eine Stunde einzusparen. Verschwenden Sie keine Zeit mit aufwändigen Priorisierungen und detaillierten ROI-Analysen. Es reicht, wenn die geplante Verbesserung einen plausiblen Beitrag zum großen Ziel leistet.
3. Schaffen Sie Kapazität. Leider heißt es allzu oft: „Grundsätzliche Verbesserungen, gut und schön, aber wir haben jetzt einfach keine Zeit für sowas“. In den drängenden Anforderungen des Tagesgeschäfts wird die geplante Verbesserung aufgerieben. Dagegen hilft nur, Kapazitäten zu reservieren und in begrenzter Zeit jeweils kleine Teile der Lösung umzusetzen: An jedem Tag wird eine halbe Stunde vor Beginn der „eigentlichen Arbeit“ (ähnlich zu Two Second Lean) für kleine Verbesserungen verwendet. Oder es gibt im Rahmen einer Aufgabe (eines Tickets) ein festes Zeitbudget, etwa eine Stunde pro Ticket.
4. Es geht nicht um Perfektion, sondern um eine messbare Verbesserung. Perfektion, wie zum Beispiel 100-prozentig automatisierte Tests, keine technischen Schulden usw., ist das Ziel, dem man sich mit einem kleinen Schritt in die richtige Richtung nähert. Dabei hilft wieder time-boxing, fragen Sie: „Was können wir im vorgegebenen Zeitrahmen von einer Stunde (einem halben Tag, zwei Tagen) erreichen?“ Es ist durchaus sinnvoll, ein Thema im Laufe von mehreren Kaizen-Maßnahmen wiederholt zu bearbeiten. Bei der Bewertung des Erfolgs empfiehlt sich ein Vorgehen nach dem PDSA-Zyklus (plan, do, study, act).
5. Unterstützen Sie die schnelle Umsetzung. Für jede Verbesserung sollte die Zeit bis zur Umsetzung kurz sein, das heißt der PDSA-Zyklus sollte möglichst schnell durchlaufen werden. Also lieber wenige Dinge auf einmal angehen, und die Mitarbeiter möglichst autonom entscheiden lassen, was sie tun und wie sie es umsetzen. Natürlich können Führungskräfte gern unterstützen, indem sie „von oben“ Hindernisse aus dem Weg räumen.
6. Wahrnehmen, Loben und Verbreiten. Das fördert die Eigendynamik und gibt den Mitarbeitern die Gelegenheit, Handwerkerstolz zu erleben. Regelmäßige Meetings wie Standups eignen sich gut dazu, fragen Sie einfach nach aktuellen Verbesserung. Hier helfen auch „Big visible charts“ um den kumulierten Effekt vieler kleiner Schritte zu visualisieren. Bei FastCap wird zu jeder Verbesserung ein kurzes Vorher-Nachher-Video gemacht, das dann beispielsweise im täglichen Standup (morning meeting) gezeigt werden kann.
7. Wiederholen. Die einzelne Verbesserung ist zwar messbar, aber klein. Durchlaufen Sie die obigen Schritte mehrmals. Vor der nächsten Runde sollte man gemeinsam kurz reflektieren: Was können wir besser machen? Reicht die Kapazität? Wen kann man noch involvieren? Wenn es gelegentliche Rückschläge gibt, ist das keine Katastrophe, denn jede Runde kostet nur wenig Zeit und sollte kaum Kosten verursachen, daher ist der Verlust begrenzt.
Kontinuität heißt auch: Es gibt kein Ende
Wenn Sie diesen Prozess einige Male durchlaufen haben, können Sie dasa schrittweise auf das nächste Thema oder Ziel erweitern, und immer mehr Mitarbeiter involvieren. Das Ziel lautet: Verbesserung jeden Tag, durch jeden Mitarbeiter, überall (Everyday Everybody Everywhere improvement – Masaaki Imai). Der KVP kennt keinen Endzustand: Prozesse, Leistungsfähigkeit der Organisation und last but not least die Fähigkeiten der Mitarbeiter – alles lässt sich immer weiterentwickeln.
*Dr. Matthias Berth unterstützt Unternehmen dabei, ihren Software-Lieferprozess zu optimieren. Er wendet dabei bevorzugt Prinzipien aus dem Lean Thinking an, um agile Vorgehensweisen zu etablieren. Der Diplommathematiker war Mitgründer und CTO einer Softwarefirma für Bioinformatik.
Be the first to comment