Mit dem Ziel einer nachhaltigen Produktion und der Verschlankung von Produktions- sowie der Optimierung von Lagerprozessen hat die ams.Solution AG gemeinsam mit dem langjährigen Kunden SSI Schäfer ein strategisches Projekt zur Weiterentwicklung der ERP-Logistikfunktionalitäten aufgesetzt. [...]
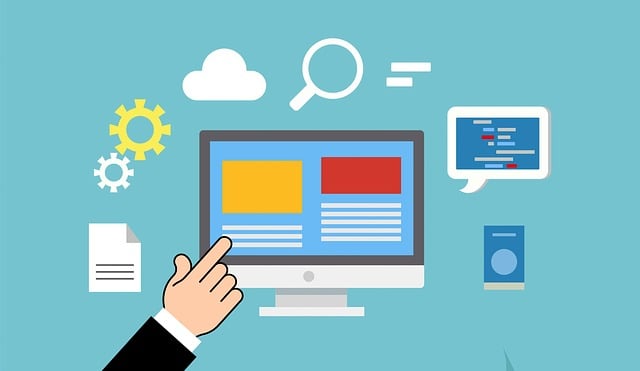
Zum einen ging es darum, die Geschwindigkeit in der Fertigung sowie den Materialfluss im Produktionsprozess zu beschleunigen, zum anderen darum, Lagerflächen zu reduzieren, Überproduktion zu vermeiden und somit Ressourcen, Kosten und Zeit zu sparen. Über den aktuellen Projektstatus sprachen wir mit dem ams-Produktverantwortlichen Jurij Schmidt.
Herr Schmidt, inwieweit ist eine ERP-Software wie ams.erp prädestiniert für die Abbildung logistischer Prozesse?
Jurij Schmidt: Die Abbildung von Logistikprozessen gehört zu unseren Kernkompetenzen, sie ist integraler Bestandteil des vernetzten, digitalen Wertschöpfungsprozesses, den unsere Kunden mit unserer Software steuern. Das Thema Logistik ist demnach kein Neuland für uns.
In ams.erp steht unseren Kunden mit der Versandsteuerung seit vielen Jahren ein mächtiges Werkzeug zur Verfügung, über das wir sehr erfolgreich alle Materialströme vom Unternehmen nach außen darstellen.
Eine funktionale Besonderheit, die unser System als Ergebnis seiner Spezialisierung auf die Losgröße 1+ mitbringt, ist die Möglichkeit des Arbeitens mit O-Teilen, also mit Artikeln ohne Artikelnummern.
Für den Logistikprozess erweist es sich als großer Vorteil, dass alle Materialien gleich behandelt werden, unabhängig davon, ob Artikel mit oder ohne Artikelnummern verwendet werden.
Warum ist dieser Aspekt so wichtig und was ist das konkrete, übergeordnete Ziel der laufenden Entwicklungsarbeit?
Jurij Schmidt: Die große Stärke des O-Teile-Managements ist in den Augen der Logistik auch ihre Schwäche. Für herkömmliche Mittel ist die Existenz einer Artikelnummer essenziell, um die Nachvollziehbarkeit der Materialbewegung zu gewährleisten.
Deswegen setzen wir bei ams auf ein von den Nutzern frei verwaltbares Platzkonzept, welches wir mit Ladungsträgern – den sogenannten Ladeeinheiten – kombinieren und so die homogene Verarbeitung von Materialien und Teilen ermöglichen.
Generell schaffen wir mit der Weiterentwicklung unserer Logistiklösung nun die Möglichkeit, nicht nur den exakten innerbetrieblichen Lagerort von Materialien zu ermitteln, sondern besitzen auch alle Informationen hinsichtlich ihres derzeitigen Zustands: Wir wissen beispielsweise, inwieweit diese Materialien bereits bearbeitet wurden oder ob eine Baugruppe fertig- oder teilfertiggestellt ist.
Das Projekt hat seinen Ursprung in der Praxis. Wie lauten die konkreten Anforderungen Ihres Kunden?
Jurij Schmidt: SSI Schäfer geht es darum, mittels einer vollumfänglichen Materialflussnachverfolgung die maximale Kontrolle über die internen Materialbewegungen zu gewinnen. Unser Kunde betreibt ein sogenanntes Konsolidierungslager mit Anlieferungen aus unterschiedlichen Quellen.
Dazu gehört zum einen ein Lager, von dem aus Material per Shuttle zum Konsolidierungslager gebracht wird, sowie zwei weitere externe Lieferanten. Aus dieser Konstellation ergibt sich, dass von einer Vielzahl an Materialien nicht bekannt ist, an welchem exakten Ort sie sich gerade befinden und ob das Material bereits vollständig in der Konsolidierungsfläche gesammelt ist.
Wir setzen auf ein von den Nutzern frei verwaltbares Platzkonzept, welches wir mit Ladungsträgern kombinieren und so die homogene Verarbeitung von Materialien und Teilen ermöglichen.
Jurij Schmidt
Die konkrete Vorgabe lautete vor diesem Hintergrund, den exakten Lagerort eines bestimmten Teiles zu einem bestimmten Zeitpunkt abzubilden. Die einzelnen Materialien sollen zudem effizienter organisiert werden können, was bedeutet, dass ermittelt wird, wann und wo welche Teile zu welchen Arbeitsschritten benötigt werden.
Wie kann dies gelingen?
Jurij Schmidt: Dies gelingt, indem man vom bisherigen Push- auf das sogenannte Pull-Prinzip umstellt. Anstelle das Material einfach auf Verdacht an die nächste Stelle in der Produktionskette weiterzuschicken (Push-Prinzip), wird es für den jeweiligen Produktionsschritt gezielt angefordert (Pull-Prinzip).
Auf diese Weise ist der Materialfluss immer nur so schnell wie die Menschen, die mit dem Material arbeiten. Dies verhindert unnötige Materialstaus und stellt sicher, dass sich Materialien stets zur richtigen Zeit am richtigen Ort befinden, ohne dabei überflüssige Lagerbestände aufbauen zu müssen.
Wie läuft die Produktentwicklung ab? In welcher Weise wird der Pilotkunde eingebunden?
Jurij Schmidt: Wir entwickeln in dem Projekt agil nach Scrum, also in sehr enger Zusammenarbeit mit SSI als Impulsgeber. In sogenannten Reviews präsentieren wir den Anwendern alle drei Wochen die neuentwickelten Features und erhalten noch während des Meetings die notwendige Rückmeldung.
Die geäußerten Punkte setzen wir im folgenden Entwicklungsschritt, dem nächsten „Sprint“, unmittelbar um – immer mit dem Fokus, eine stimmige Standardsoftware zu präsentieren.
Welche sind die nächsten Schritte?
Jurij Schmidt: Wir denken im Rahmen der Weiterentwicklung nicht mehr nur in festen Orten, sondern auch in mobilen. Dies bedeutet, dass wir beispielsweise auch Transportfahrzeuge einbinden können, die nicht nur innerbetrieblich, sondern auch außerhalb unterwegs sind.
Eine mögliche Variante zur Umsetzung in der Praxis könnte dabei sein, innerbetriebliche Checkpoints zu definieren, an denen mithilfe von RFID-Chips oder Scans Material, das eine Kreuzung oder ein Regal passiert, mit Koordinaten versehen wird und so exakt lokalisiert werden kann.
Denkbar wäre zudem die Platzierung von GPS-Trackern an den Fahrzeugen, um eine genaue Nachverfolgung zu ermöglichen. Unsere Vision von Logistik könnte man wie folgt formulieren: die einfachste und präziseste Verortung von Materialen an allen denkbaren Standorten in Echtzeit.
Herr Schmidt, wir danken für das Gespräch.
Be the first to comment