Die Einführung von auf Daten basierten Services und digitalen Prozessen im Rahmen des Internet of Things (IoT) ändert Instandhaltungsprozesse erheblich und bietet zusätzlichen Nutzen. [...]
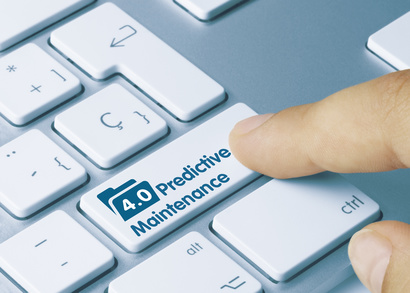
Die nächste Generation Mitarbeiter ist es gewohnt, auf alle Fragen eine schnelle Antwort zu bekommen. In den Werkshallen treffen sie auf die nächste Generation von Produktionsmaschinen. Diese stellen immer mehr Daten bereit und sind an das Unternehmensnetzwerk angebunden – durch einfache IT-basierte APIs (Application Programming Interfaces) anstatt komplexen Maschinenanbindungen. Sensoren innerhalb der Maschinen liefern Echtzeitdaten, die wiederum über Apps quasi in Echtzeit dargestellt werden. Das HMI (Human-Machine-Interface) der Maschinen wird einfacher in der Bedienung. Somit stehen dem Operator von Maschinen heute viel mehr Daten zur Verfügung als noch vor fünf bis zehn Jahren. Jede neue Maschine wird nun vernetzt und bietet Datenströme an.
Predictive Maintenance statt fester Wartungsintervalle
Die Vernetzung verändert auch die Art und Weise, wie die Instandhaltung von Maschinen abläuft. So ergänzen Hinweise nun die üblicherweise fest eingeplanten, regelmäßigen Wartungsintervalle für eine Maschine. Dazu werden die von der Maschine kommenden Daten erfasst und ausgewertet – entweder direkt an der Maschine (Edge) oder in der mit dem Service verbundenen Cloud. Das geschieht wie folgt: der Maschinennutzer setzt in der App Grenzwerte für ausgewählte Daten fest. Zum Beispiel auf Stanzkraft, Temperatur, Schwingung, etc. Nun wird bestimmt was passieren soll, wenn eine Abweichung von den Grenzen erfolgt.
Solche Alarme informieren relevante Personen im Unternehmen beispielsweise über eine E-Mail oder SMS darüber, dass hier eine vorbeugende Instandhaltung (Predictive Maintenance) angebracht ist. Schon ist die erste Stufe vorbeugender Instandhaltung in Abhängigkeit von der Maschinennutzung möglich.
Die Analyse von Maschinenstillständen ist sehr wichtig. Häufen sich beispielsweise bestimmte Stillstandstypen, so muss der Betriebsleiter Maßnahmen ergreifen, um die Produktion mit der gewünschten Effizienz und Leistung am Laufen zu halten. Heute ist es üblich, Stillstandszeiten per Hand in ein BDE-System (Betriebs-Daten-Erfassung) einzugeben. Kommt es zu einem Stillstand, muss der Operator den Stillstand dokumentieren. Das verbraucht Zeit und erfordert viel Fachwissen, weil es ja auch gilt, den Grund des Stillstandes anzugeben.
Maschinen werden auskunftsfreudiger
Moderne Maschinen dokumentieren ihre Stillstände automatisch. Eine Auswertung der Stillstände kann dann via App mithilfe einer Pareto-Analyse oder elektronischer Grafiken und Listen erfolgen. Das hat gleich zwei wesentliche Vorteile für die Instandhaltung: Erstens wird der Operator von der Dokumentation befreit und kann sich ganz auf die Lösung des Problemes konzentrieren. Zweitens können anhand der von der Maschine dokumentierten Stillstände detailliere Auswertungen erfolgen und so Rückschlüsse auf die Ursachen gezogen werden.
Beispielsweis deutet eine höhere Stanzkraft bei einer Flachbettstanze für den immer wiederkehrenden gleichen Job auf einen ansteigenden Verschleiss der Stanzwerkzeuge hin. Werden beispielweise immer öfter Einzugsprobleme von Wellpappenstücken gemeldet, so kann das Rückschlüsse auf eine falsche Materiallagerung oder -klimatisierung zulassen. Mit Hilfe von Stillstandsanalysen von Schichten und Produkten, die gefertigt werden, konnte schon vielen Betrieben dabei geholfen werden, ihre Instandhaltungsprozesse zu optimieren.
Neue Remote-Services sind möglich
In einem nächsten Schritt können auf Daten basierende Services noch weiter gehen. Bisher ruft der Maschinenbetreiber immer im letzten Moment den Service des Maschineherstellers an. Wie wäre es, wenn der Service sich beim Kunden meldet? Ist das der Weg, in Zukunft proaktiv Stillstände zu vermeiden? Neben einer Vielzahl wichtiger Daten spielt die Tatsache eine Rolle, dass die Maschinen bei vorhandener Vernetzung auch den Fernzugriff unterstützen. Das bedeutet, ein Techniker kann aus der Ferne auf die wesntlichen Funktionen der Maschinen zugreifen und die Instandhaltung vor Ort unterstützen. Das reduziert die Wartezeit, bis ein Techniker vor Ort kommen kann. Darüber hinaus kann bei Verwendung von Datenbrillen mit Augmented Reality ein direktes Eingreifen vor Ort aus der Ferne unterstützt werden.
Zusammengefasst gesagt ergeben die Auswirkungen zusätzlichen Nutzen im Betrieb vor Ort:
- Alarme helfen, schneller Instandhaltungsbedarf zu erkennen;
- automatische Erfassung und Dokumentation von Maschinenstillständen sparen wertvolle Zeit;
- Auswertungen via App bzw. Reports finden Ursachen und ermöglichen so eine Optimierung der Fertigung;
- proaktive Services und Remote Service verkürzen die Stillstandszeiten;
- neue Serviceangebote unterstützen die lokale Instandhaltung im Betrieb vor Ort
Auf dem Weg zu Smart Machines
Mithilfe von Daten können wir heute schon Grenzen setzen, beobachten, alarmieren und notwendige Sichten erstellen. Nun gilt es, aus der Analyse der Daten in Zukunft Entscheidungen abzuleiten. Daraus resultieren dann Handlungsvorschläge. Ein zukünftiger Algorithmus für vorbeugende Services sollte mindestens die folgenden Komponenten beinhalten:
- Digital Twin (SOLL-Zustand)
- Historische Daten (Erfahrung)
- Umgebungs- bzw. Produktionsdaten (Umgebung, Nutzung, was wurde in welchem Kontext produziert)
- aktuelle Betriebsdaten (IST-Zustand)
Erste Beispiele für vorbeugende Instandhaltung rein auf Datenbasis gibt es bereits. Jedoch befinden wir uns hier auf dem Weg zu weiterer Automatisierung, auf dem Weg zu intelligenten Maschinen (Smart Machines). Maschinen werden lernen (Machine Learning) und uns mit künstlicher Intelligenz (KI) unterstützen. Im IT Glossary von Gartner werden Smart Machines als Maschinen bezeichnet, die selbst lernen und unvorhergesehene Ergebnisse bringen können. Wir sind gespannt darauf!
* Als Product Specialist Connected Services (IOT Services) bei der Bobst Meerbusch GmbH unterstützt Manfred Bauer Kunden der Verpackungsindustrie in Europa bei der Einführung digitaler Prozesse.
Be the first to comment