Der Austausch von Produktionsdaten hat sich dramatisch weiterentwickelt und steht kurz davor, sein transformatives Potenzial voll auszuschöpfen. Lesen Sie hier, wie Menschen und Maschinen in Echtzeit interagieren, um die richtigen Daten zu übermitteln und Fertigungsprozesse zu transformieren. [...]
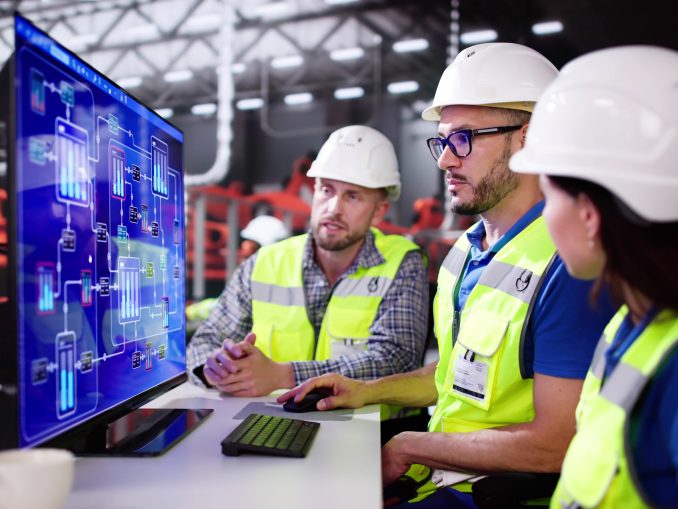
Vom 3D-Druck bis hin zur künstlichen Intelligenz – Fertigungsprozesse befinden sich im Umbruch. Und nun gibt es erstmals eine Technologie, die es den Herstellern ermöglicht, ihre Prozesse nicht vom Teil zum Produkt mit allen Unterbrechungen dazwischen zu betrachten, sondern umgekehrt vom Produkt zum Teil, und das in Echtzeit.
Der Austausch von Produktionsdaten hat sich dramatisch weiterentwickelt und steht kurz davor, sein transformatives Potenzial voll auszuschöpfen. Alles begann mit Industrie 3.0, als Fabriken nach und nach Konnektivität einführten und zentralisierte ERP-Monolithen verschiedene Aspekte des Systems miteinander verbanden. Die Fertigung unternahm die ersten einfachen Schritte, um den Datenfluss zu verstehen und zu integrieren.
Nachdem diese Digitalisierung in Gang gesetzt worden war, kam Industrie 4.0 auf, bei der das zentralisierte ERP-System modularer wurde. Das war ein Wendepunkt auf dem Weg zum Verständnis von Daten in Bewegung. Denn die Welten der Informationstechnologie (IT) und der Betriebstechnologie (OT) begannen, sich miteinander zu integrieren und Informationen auszutauschen – zum Beispiel in Manufacturing Execution Systems (MES), SCADA-Systemen und historischen Fehlererkennungssysteme in den Werken.
Die Wiederentdeckung des Faktors Mensch in der Produktion
Ausgehend von Industrie 4.0 bewegen wir uns nun in Richtung Industrie 5.0. In einem Policy Brief der Europäischen Kommission wird das Ziel von Industrie 5.0 so definiert: „Über Effizienz und Produktivität als alleinige Ziele hinauszugehen und die Rolle und den Beitrag der Industrie für die Gesellschaft zu stärken.“ Industrie 5.0 soll den bestehenden Ansatz von Industrie 4.0 ergänzen, indem es Forschung und Innovation gezielt für den Übergang zu einer nachhaltigen, auf den Menschen ausgerichteten, widerstandsfähigen Fertigungsindustrie einsetzt.
Auch nordamerikanische Unternehmen sehen die menschliche Arbeitskraft im Mittelpunkt von Industrie 5.0, wobei das Unternehmenswachstum durch eine Kombination von Innovation und Humankapital vorangetrieben wird. Darüber hinaus besteht die dringende Notwendigkeit, KI zu nutzen und gleichzeitig den Menschen in den Mittelpunkt zu stellen sowie Nachhaltigkeit und Widerstandsfähigkeit zu gewährleisten. Das erfordert ein technisches Gleichgewicht, damit Mensch und Maschine zusammenarbeiten und voneinander lernen können.
Der Weg zu dieser Harmonie beginnt auf der Datenebene. Industrie 5.0 führt zu einer stärkeren Verzahnung von IT und OT – durch die Aggregation von Betriebsdaten in Echtzeit, die kontinuierliche Erfassung und Analyse von Daten und die Bereitstellung eines umfassenden Überblicks über den Produktionsprozess. Diese Daten können dann allen relevanten Beteiligten, insbesondere den Mitarbeitern in der Produktion, zur Verfügung gestellt werden, damit sie wichtige Entscheidungen auf der Grundlage präziser Echtzeitdaten treffen können.
Neuer Ansatz für den Datenaustausch erforderlich – mit neuen Enablern
Stellen Sie sich eine Welt vor, in der Geschäftsprozesse nicht mehr durch Verzögerungen oder Engpässe behindert werden. Und zwar nicht nur in der Fabrikhalle, sondern im gesamten Unternehmen und in allen Geschäftsbereichen. Wie wäre es, wenn Sie alles miteinander verknüpfen könnten, selbst wenn Sie im Front- und Backoffice verschiedene Systeme für das Produktionsmanagement einsetzen?
Dabei kann es sich um Systeme der OT-Schicht handeln, die mit Systemen der IT-Schicht in einer sicheren, garantierten und gedrosselten Multisite- und Cloud-Umgebung über mehrere Standorte hinweg in Echtzeit kommunizieren. Auf diese Weise werden operative Systeme wie MES, speicherprogrammierbare Steuerungen (SPS), SCADA-Systeme und OPC Unified Architecture (OPC UA) Schichten bidirektional mit Stammdaten, Product Lifecycle Management (PLM), Customer Relationship Management (CRM) und Incident-Management-Systemen von SAP, Salesforce, ServiceNow, Microsoft, Oracle und vielen anderen Herstellern verbunden.
Alle diese Systeme können für eine Vielzahl von Anwendungsfällen in der Fabrik, im Lager und in der Logistik nahtlos miteinander verbunden werden. Um das zu ermöglichen, muss sich die Integration neu erfinden, insbesondere wenn sie andere Technologien einbeziehen soll, die in der Fabrik auf dem Vormarsch sind, wie zum Beispiel künstliche Intelligenz. Damit diese von Industrie 5.0 und KI geprägte Welt Wirklichkeit werden kann, müssen wir umdenken.
Der Beginn eines Event-Mesh in der Produktion
Lockerer werden: Dieses Umdenken erfordert ein viel moderneres Verständnis von Integration. Wir müssen aufhören, eine traditionelle Batch-Historie mit Updates oder einen Enterprise Service Bus (ESB) als Architektur einzusetzen, bei der eine zentrale Softwarekomponente die Integration zwischen Anwendungen übernimmt. Vielmehr müssen wir zu einem lockeren, ereignisgesteuerten Ansatz für den Datentransfer übergehen. In Bezug auf die Enabler ist das die Grundlage von Industrie 5.0.
Was man sät, das erntet man: Eine Anwendung sendet Nachrichten oder Ereignisse, andere Anwendungen empfangen diese Events. Neue Anwendungen oder Geräte kommen hinzu, sie beginnen, die Daten zu empfangen, und neue Daten fließen zu ihnen. Das Hinzufügen weiterer Anwendungen erfolgt völlig nahtlos.
Daten fließen: Dadurch können Fertigungsunternehmen den Datenaustausch zwischen Geräten und Sensoren so erweitern, dass alle Arten von Sensoren Informationen veröffentlichen oder abonnieren können. Ein Beispiel ist der Ausfall einer Produktionslinie. Das ist ein Ereignis auf der OT-Seite des Unternehmens. Die einzige Möglichkeit, herauszufinden, welche Kunden und Elemente der Lieferkette betroffen sind, besteht darin, dieses OT-Ereignis mit allen anderen IT-Systemen – ERP, CRM, Transportmanagement, Logistik usw. – zu verknüpfen. Stellen Sie sich vor, Sie könnten das Ereignis „Produktionslinie ausgefallen“ in Echtzeit an die verschiedenen IT-Systeme weiterleiten: Wie viel Transparenz würde das bringen und wie schnell könnte auf das Ereignis reagiert werden!
Ein Event-Mesh entsteht: Ein Event-Mesh verbindet verschiedene Systeme – IT, OT, KI – effizient als universelle Konnektivitätsschicht. Es ermöglicht die Integration einer Vielzahl von Geräten, die Verbindung von Anlagen und Logistik und die Fähigkeit, all das zu steuern und alle Events in Echtzeit zu verstehen. Echtzeit ist hier entscheidend, da es sich bei Ereignissen um unmittelbare „Vorkommnisse“ handelt, sei es auf der IT-Seite oder auf der OT-Seite. Mithilfe eines Event-Mesh können wir jedes Ereignis im Detail betrachten und stellen fest, dass es mithilfe von „Topic Routing“ als Objekte + Aktionen + Eigenschaften dargestellt werden kann. In unserem Beispiel: „Produktionslinie“ (Objekt) + „ausgefallen“ (Aktion) + „in Region X, in Werk Y, Linie Z“ (Eigenschaften).
Ein Event-Mesh leitet diese Ereignisse in Echtzeit garantiert an alle interessierten und entsprechend „eingestellten“ Anwendungen und Systeme weiter. Die Anwendungen sind entweder nativ mit dem Event-Mesh verbunden, wie z.B. SAP, OPC UA über MQTT, oder sie verbinden sich über Mikrointegrationen, also einfache Konnektoren, die es Legacy-Anwendungen ermöglichen, sich mit dem Mesh zu verbinden, um Ereignisse zu erzeugen oder zu konsumieren.
KI und das Metaversum in der Fabrik der Zukunft
Wie EY betont, hat das industrielle Metaversum das Potenzial, Produktionsprozesse zu revolutionieren und deren Management zu optimieren. Ermöglicht wird das durch datengesteuerte digitale Zwillinge, Modellsimulationen und Datenanalysen, die den Weg für neue Arbeitsweisen ebnen. Ein Beispiel hierfür ist Nvidia Omniverse.
Das Metaversum muss in Echtzeit mit dem physischen Universum verbunden sein. Es ist jedoch zu kosten- und energieintensiv, KI-Modelle in Echtzeit zu trainieren. Wie können wir also KI mit Echtzeitdaten integrieren? Indem wir Agentic AI und Retrieval-Augmented Generation (RAG) einsetzen, um GenAI-Fähigkeiten mit Echtzeitdaten zu verknüpfen. Bei diesen Echtzeitdaten handelt es sich im Wesentlichen um Ereignisströme auf dem Event-Mesh, die in Agents- oder RAG-Vektordatenbanken einfließen und diese mit Echtzeitkontext auf dem neuesten Stand halten.
Die ereignisgesteuerte Integration ermöglicht es Fertigungsunternehmen, sich an all diese Veränderungen in der Fabrikhalle anzupassen, neue Technologien wie KI-Modelle besser zu nutzen oder sich mit den wachsenden industriellen Metaversum-Anwendungen in der Fertigung zu verbinden. Der Wegbereiter für KI ist ein ereignisgesteuerter Integrationsmechanismus, der die KI in autonomen Systemen über ein sogenanntes „Kontext-Mesh“ mit Echtzeitkontext versorgt.
Ein Kontext-Mesh vereint den gesamten Kontext eines Unternehmens, der als Grundlage für anspruchsvolle KI-Anwendungen dienen kann – von intelligenten Assistenten, die GenAI-Modelle und komplexe Analysewerkzeuge nutzen, über maschinensprachliche Empfehlungsmodelle bis hin zu maßgeschneiderten KI-Anwendungen, die Deep Learning oder Reinforcement Learning nutzen. Das überträgt den Echtzeitkontext auf die digitalen Zwillinge.
Echtzeit-Anwendungsfälle aus der Fertigung
Ein führendes multinationales Engineering- und Technologieunternehmen nutzt ereignisgesteuerte Integration, um seine weltweiten Produktionsstandorte miteinander zu verbinden. Konkret hat der Hersteller in jedem seiner 160 Werke sowie in seinen IT-Schichten vor Ort und in der Cloud Event-Broker implementiert, die ein großes, verbundenes Event-Netz bilden.
Stammdatenverwaltung in großem Maßstab
Mit Hilfe eines Event-Mesh konnte das Unternehmen die Verteilung großer Mengen von Produktstammdaten im gesamten Unternehmen optimieren.
In den weltweiten Werken werden 7.000 Teile pro Minute produziert. Dafür musste das Unternehmen die Produktionsstammdaten, wie z. B. die Hauptstückliste, an mehrere Produktionsstandorte senden. Das bedeutete, dass täglich 6.000.000 Nachrichten, was einem Datenvolumen von drei Terabyte entspricht, an verschiedene Werke weltweit übermittelt werden mussten.
Wenn diese Produkte in weiteren Fabriken hergestellt werden oder sich die Stammdaten ändern, werden die Datenanforderungen immer umfangreicher und komplexer – was zu einem riesigen End-to-End-Szenario führt.
Mit Hilfe eines Event-Mesh kann das Unternehmen nun die Produktionsmasterdaten in Echtzeit an alle erforderlichen Umgebungen übertragen. Das stabile asynchrone Netzwerk zwischen den zentralen Rechenzentren in aller Welt und den verschiedenen Produktionsstandorten ermöglicht die Vernetzung von Fabriken auf der ganzen Welt.
Einsatz von KI zur Fehlerminimierung
Dieses Unternehmen konnte KI auch in allen Produktionslinien einsetzen, um die Fehlerquote auf weniger als ein Teil pro zehn Millionen produzierter Teile zu senken. Das Unternehmen möchte nun die Produktionslinien mit verschiedenen Modellen beschleunigen und die Fehlerquote weiter senken.
Durch den Einsatz eines ereignisgesteuerten Integrations-Backbones zur Unterstützung der Datenanforderungen neuer KI-Modelle will das Unternehmen seine Erfolgsquote in der Produktion weiter steigern. Der Hersteller geht davon aus, dass er die Fehlerquote in Zukunft auf ein Teil pro 100 Millionen produzierter Teile minimieren kann.
Die Integration der Produktion erfordert ein Umdenken
Auf dem Weg zu Industrie 5.0 reichen traditionelle Integrationsmethoden nicht mehr aus. Grundlage von Industrie 5.0 ist die nahtlose Zusammenarbeit von Mensch und Maschine, die durch den Datenaustausch in Echtzeit erleichtert wird.
Die ereignisgesteuerte Integration ist ein entscheidender Faktor, um das volle Potenzial von Echtzeitdaten in der globalen Fertigung auszuschöpfen. Die Technologie ist vorhanden – und die Menschen spielen dabei eine Rolle!
* Sumeet Puri ist Chief Technology Solutions Officer bei Solace.
Be the first to comment