Auf der Hannover Messe Ende April war das Schlagwort Industrie 4.0 wieder beherrschendes Thema. Die COMPUTERWELT hat fünf heimische Experten befragt, was Industrie 4.0 tatsächlich bedeutet, welche Use Cases es gibt und wohin die Reise geht. [...]
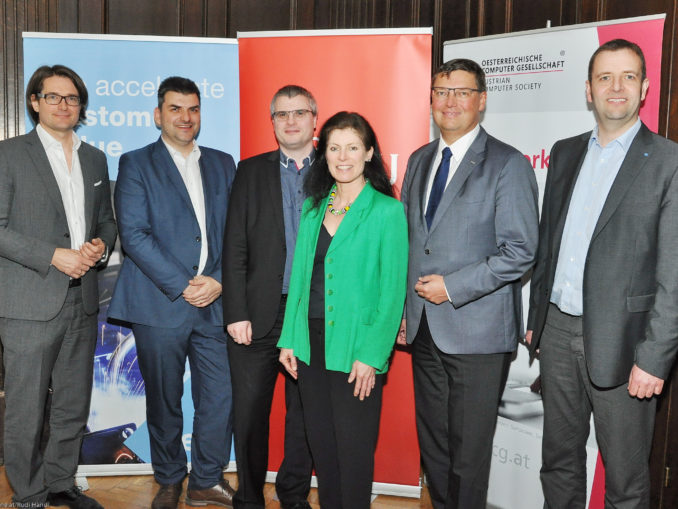
Themen wie Industrie 4.0 und IoT beschäftigen uns bei SAP schon lange. Mit dem neuen digitalen SAP-Innovationssystem Leonardo, das zahlreiche zukunftsorientierte Technologien wie Analytics, Machine Learning, Blockchain und AI beinhaltet, gibt es nun eine neue Zugangsweise, mit der wir Unternehmen dabei unterstützen, die digitale Transformation zu bewältigen und rasch zu Einführung von digitalen Innovationen zu kommen. Wir sind auch Partner der Pilotfabrik Industrie 4.0 und arbeiten hier mit der TU Wien und anderen Partnern am Zusammenführen der physikalischen Welt mit deskriptiven Systemen«, leitet Christoph Kränkl, Bereichsleiter Industrie bei SAP Österreich, die Gesprächsrunde ein.
Mit der Produktionsforschung seit vielen Jahren befasst ist Detlef Gerhard. Er leitet seit zwölf Jahren den Forschungsbereich Maschinenbauinformatik und Virtuelle Produktentwicklung der TU Wien und ist dort seit einigen Jahren auch Dekan der Fakultät für Maschinenwesen: »Gemeinsam mit meinen Kollegen Professor Bleicher und Professor Sihn habe ich die Pilotfabrik Industrie 4.0 aufgebaut. Da setzen wir mit unseren Teams im Wesentlichen drei Dinge um: Einerseits Lehre zu unterstützen, also Dinge begreifbar zu machen, zweitens Forschung im Bereich intelligenter Produktionssysteme – auch hier geht es um konkrete Umsetzung – und drittens Technologietransfer, hier ist die Kooperation mit den Industriepartnern am deutlichsten. Da entwickeln und implementieren wir gemeinsam mit Industriepartnern Lösungen, damit wollen wir gerade auch KMU Anregungen geben, wie sie das Thema Industrie 4.0 in ihrem eigenen Umfeld umsetzen können«, zählt Gerhard auf.
»Wir haben die Entscheidung getroffen, Industrie 4.0 als eines der Fokusthemen in Österreich aus dem riesigen Portfolio des Fujitsu-Konzerns herauszunehmen – schon allein deswegen, weil wir der letzte Hersteller sind, der noch ein Werk in der Region hat. Das Werk in Augsburg in Deutschland existiert nur deshalb, weil wir genau dort Industrie 4.0 schon seit rund fünfzehn Jahren ganz konkret umsetzen«, betont Josef Höckner, seit zwei Jahren CTO bei Fujitsu Österreich. Das Fujitsu-Werk in Augsburg, wo nach wie vor Server und Laptops produziert werden, gilt als Musterschüler und Pionier in punkto Industrie 4.0. »Darüber hinaus übernehmen wir viele Themen, die in Japan forciert werden, und transferieren dieses Knowhow mehr und mehr nach Europa«, fügt Höckner hinzu.
Komplexe Thematik und Herausforderungen
»Wenn wir über die Use Cases sprechen, dann müssen wir uns darüber unterhalten, dass vieles, was wir heute Industrie 4.0 benennen, schon seit fast 20 Jahren state of the art ist«, bringt Christian Hofmann, beim IT-Servicedienstleister Tieto für den Manufacturing-Bereich verantwortlich, das Gespräch auf die Begriffsdefinition. Hofmann, der auch viele Jahre bei Tieto in Finnland & Schweden verbracht hat, stellt zudem fest, dass »Skandinavien in punkto Industrie 4.0 in meiner Wahrnehmung gegenüber Zentraleuropa zwei, drei Jahre voraus ist.« Hofmann agiert auch als Leiter der Expertengruppe »Neue Geschäftsmodelle« der heimischen »Plattform Industrie 4.0«. Diese Expertengruppe wurde 2018 im Rahmen der Plattform Industrie 4.0 gegründet, »weil das der logische nächste Schritt ist, von der Produktionsoptimierung hin zu Smart Products und Outcome-based-Modellen«, erklärt Hofmann.
Prozessautomatisierung wird ja schon seit Jahrzehnten betrieben, aber was ist nun das Neue an Industrie 4.0, wozu braucht es eine Pilotfabrik und was passiert dort tatsächlich? »In der Pilotfabrik Industrie 4.0 versuchen wir die Dinge, die in der Prozessindustrie schon seit einiger Zeit umgesetzt sind, auch für die diskrete Fertigungsindustrie anwendbar zu machen, wobei auch in der Prozessindustrie der wesentliche Fokus auf dem Optimieren des Prozesses liegt. Neu ist, dass über entsprechende Sensorik sehr viele Daten verschiedener Maschinen eines Produktionssystems erfasst werden, dass man damit die Produktivität und den Automatisierungsgrad in der diskreten Produktion verbessern kann«, sagt Gerhard. Neben dem Thema Optimierung gibt es noch weitere Aspekte, »so schauen wir etwa die Betriebsphase von Maschinen für Smart Maintenance Fragestellungen an, und wir haben das Ziel, Daten aus den unterschiedlichen Lebenszyklus-Phasen wieder zurückzuführen im Sinne von Qualitätsmanagement. Das heißt, dass wir Erkenntnisse aus dem Betrieb eines Produkts verwenden, um Schwächen des Produkts zu erkennen und in der Produktentwicklung zu beheben. Wesentlich ist der Unterschied, dass wir versuchen, unterschiedliche Systemkomponenten der Produktion miteinander in Beziehung zu bringen und die Daten dann zu analysieren, daraus Schlüsse zu ziehen und daraus Verbesserungen zu generieren«, stellt Gerhard fest. Die Pilotfabrik wurde 2015 initiiert und 2016 offiziell eröffnet, rund 20 Industriepartner sind beteiligt. Jetzt geht es konkret darum, ganzheitliche Industrie-4.0-Use-Cases zu zeigen und angreifbar zu machen: »Wir haben jeden Donnerstag Demo-Produktionsbetrieb, hier kommen interessierte Firmen, aber auch Schulklassen. Darüber hinaus haben wir auch einen Open Lab Day zwei Mal pro Jahr, wo gebündelt Use Cases gezeigt werden. Anhand dieser Use Cases kann man sich sicher gute Anregungen holen«, so Gerhards Einladung an alle Interessierten.
Problem: Heterogene Maschinenwelt
»In der Industrie-Automatisierung sehen wir, dass gerade ein Paradigmen-Wechsel stattfindet: weg von einer stark segmentierten, auf proprietären Technologien aufgebauten Welt hin zu offenen Standards«, betont Wolfgang Leindecker, für Marketing und Vertrieb im Bereich Industrie bei TTTech verantwortlich. TTTech, in der Öffentlichkeit vor allem durch wesentliche Beiträge zum autonomen Fahren bekannt, wurde 1998 als Spinoff der TU Wien gegründet und agiert heute mit mehr als 600 Mitarbeitern weltweit als Technologieführer im Bereich vernetzte Sicherheitssteuerungen, die in selbstfahrenden Autos, in der Luft- und Raumfahrt, in der Energieproduktion sowie für industrielle Prozessautomatisierung zum Einsatz kommen.
Besonders augenscheinlich wird diese Veränderung laut Leindecker in der heterogenen Maschinenwelt einer typischen Produktionsumgebung: »Es gibt heute rund zehn verschiedene relevante Ökosysteme für die industrielle Kommunikation und es ist beinahe unmöglich, Maschinen aus den unterschiedlichen Welten sinnvoll miteinander zu verbinden. Maschinenbauer müssen viel investieren, um sich an diese unproduktive Vielfalt anzupassen. Für eine selbstoptimierte Produktion ist es essentiell, dass Maschinen interoperabel werden und sich gegenseitig auf Anhieb verstehen. Genau das liefert der Kommunikationsstandard OPC UA auf Basis von TSN-Netzwerken für die Echtzeit-Vernetzung«.
TTTech setzt auf diesen Standard und hält fertige Lösungen parat: »Wir entwickeln Hightech-Lösungen und passen sie an verschiedenste Märkte an. Wir müssen da ungefähr zehn, fünfzehn Jahre voraus entwickeln, damit die Technologien Marktreife erlangen und letztlich in Serien-Produkte hineinkommen können«, erklärt der TTTech Manager.
Das Schlagwort Industrie 4.0 sieht er im Begriff Industrial IoT verdichtet: »Industrial IoT heißt, dass die klassische IT-Welt mit der OT-Welt – das ist die Automatisierungswelt, die Steuerungs- und Feldbus Welt – zusammenwächst, also Konvergenz von IT und OT. Das funktioniert auch als nettes Wortspiel und ergibt dann IoT«, so Leindecker und setzt mit einem Vergleich fort: »Das ist etwa so wie vor 20 Jahren: Damals hatten wir die Telekom/Voice-Welt und die Netzwerk- und IT-Welt. Dann kam Voice over IP und die beiden Welten wurden mit einer Reihe von neuen Anwendungsmöglichkeiten verschmolzen. Genau das Gleiche passiert jetzt aus meiner Sicht hier.«
In der Praxis laufen eine Reihe von Bestrebungen in diese Richtung ab. So hat sich eine Gruppe von Branchenführern rund um ABB, Belden, Bosch Rexroth, B&R, Cisco, Hilscher, KUKA, National Instruments, Phoenix Contact, Pilz, Schneider Electric, TTTech und WAGO zusammengetan (zusammen als »Shapers« bekannt), um eine Kommunikationslösung für Echtzeit- und Sensor-to-Cloud-Anwendungen im industriellen Umfeld zu entwickeln. Zur Hannover Messe 2018 wurde diese Gruppe noch um Rockwell Automation erweitert. Siemens hat in Hannover ebenso Steuerungen auf Basis von OPC UA über TSN gezeigt. Damit hat sich ein Großteil des Weltmarktes bereits auf die neue Welt der Offenheit verständigt.
Der Mensch im Mittelpunkt
»Es gibt schon sehr, sehr viele Ansätze, wo Unternehmen bereits begonnen haben, verstärkt in die Digitalisierung und Industrie 4.0 einzusteigen, in die Abbildung der Realität in der digitalen Welt. Man hört sogar immer wieder die Meinung: ,Wir tun das schon sehr lange, etwa mit modernen Fertigungsstraßen und der damit verbundenen Optimierung.‘ Und das ist auch richtig. Aus unserer Sicht entwickeln sich aber gerade jetzt sehr viele neue Ideen und Geschäftsmodelle. Wir empfehlen dabei, immer vom User oder Kunden her zu denken. Und Kunde ist nicht immer der Unternehmenskunde, sondern jeder, der in der Wertschöpfungskette mit einem digitalen Prozess in Berührung kommt. Im Industrie-4.0-Zeitalter benötigen Hersteller intelligente, vernetzte Lösungen, die vorausschauende Methoden ermöglichen. Speziell unsere Lösungen für die Fertigung helfen Kunden, vom Industrial IoT zu profitieren, denn sie verbinden Geräte, Personen und Prozesse in der erweiterten, digitalen Lieferkette. Außerdem sorgen sie dafür, dass Produktions- und Geschäftsabläufe eng miteinander verknüpft werden«, fasst Kränkl zusammen.
Stammdaten als Bremse
»Das zweite Thema, mit dem sich die Kunden intensiv beschäftigen, sind die Stammdaten in den IT-Systemen. Denn die Eindeutigkeit dieser Stammdaten – egal ob Kunden- und Lieferantenstamm, Materialstamm oder Equipment-Nummern – ist die Basis für alle Digitalisierung. Bei einem Kundenbesuch hörte ich: Es ist toll, dass wir mit Drohnen über unsere Anlagen fliegen können, wir fotografieren auch unseren Lagerbestand – aber es nützt uns nichts, weil dahinter die Stammdaten noch nicht so verfügbar sind, dass damit Ersatzteile oder Verbrauchsteile direkt bestellt werden können. Damit sind wir von Predictive Maintainance noch weit entfernt«, schildert Kränkl eine ganz konkrete Situation. Und weiter: »Wir sehen, dass die technische Innovation in der Fertigung zwar massiv vorwärts geht und es gibt im Moment sehr viele experimentelle Inseln und Pilotversuche, aber wir erleben es genauso oft, wenn es dann um die Abdeckung der komplette Prozesskette geht, dass dann oft die Erkenntnis in vielen Unternehmen da ist: Das müssen wir erst hinbauen bzw. ordentlich abbilden. Und das sind Eingriffe, die gehen nicht im Zeitraum weniger Wochen, sondern die werden die Unternehmen die nächsten Monate intensiv beschäftigen,« schätzt Kränkl.
»Man darf nicht vergessen, dass das Thema Industrie 4.0 kein Evolutions-, sondern ein Revolutions-Thema ist. Überall auf der Welt brechen wir gerade komplette Produktionsstrukturen auf. Da liegt viel Chance drinnen, aber auch wahnsinnig viel Veränderung. Die Unternehmen sind teilweise noch gar nicht dafür gebaut, damit umgehen zu können«, betont Josef Höckner. Das Thema müsse jedenfalls vom Vorstand bzw. Management des Unternehmens getragen werden und sei sehr komplex: »Kein Unternehmen ist derzeit in der Lage, das Thema Industrie 4.0 vollinhaltlich abdecken zu können – das gibt es derzeit nicht«. Höckner rät Unternehmen, »nicht sofort alles über Bord zu werfen, sondern einmal zu nutzen, was vorhanden ist – Industrieanlagen haben nun einmal nicht eine Nutzungszeit von nur drei Jahren, die werden länger genutzt. Daher gilt es Wege zu finden, mit all diesen Anlagen eine Gesamtlösung zu bauen – das kann kein einzelner. Da geht es darum, die notwendige Microservice Architektur aufzubauen, da geht es um das Thema Zusammenarbeit und ich muss mir Gedanken aus User-Sicht machen. Einige Unternehmen haben das schon erfolgreich vorgezeigt, das bekannteste ist sicher Amazon, weil es genau aus diesem Verständnis des Bedienens der Bedürfnisse des Users perfekt agiert, mit einer ganz anderen Struktur, wie wir in Europa Unternehmen führen«, gibt Höckner zu bedenken. »Da ist bei uns noch wahnsinnig viel Umdenken notwendig, da ist noch viel an Veränderung auch in den Modellen der Arbeitswelt notwendig, da haben wir noch ein gutes Stück Weg zu gehen«, sieht Höckner auch noch große organisatorische Herausforderungen. »Aber es ist für Europa eine der größten Chancen, die wir in den nächsten Jahren haben, weil das Thema der Kosten der Manpower in Europa in solch einer Lösungsumgebung nicht mehr so eine große Rolle spielt.« Andrerseits liegen »rund 60 bis 70 Prozent des IoT-Marktes in Asien – dort finden die großen Entwicklungen statt, dort müssen wir unseren Blick hinrichten«, sagt Höckner.
Prozess-Knowhow und Losgröße EINS
Christian Hofmanns Replik darauf: »Optimismus braucht das Land! Es wird zu viel Angstmache um das Phänomen Industrie 4.0 betrieben.« Hofmann sieht zwei Treiber: »Industrie 4.0 bietet Produktionsunternehmen die Chance, die erfahrenen Maschinenbediener, die 20 Jahre gelernt haben, Optimierungen in einer Fabrik zu machen und die jetzt langsam in den Ruhestand gehen, mit modernen Werkzeugen auszustatten. Es geht darum, dieses Prozess-Knowhow zu bewahren und neue Optimierungsmöglichkeiten faktenbasiert zu bewerten. Der zweite Treiber ist Losgröße EINS – und ich denke, dass der Anteil an Kundeneinzelfertigung, sowohl für die Produktion, als auch für das anschließende Servicegeschäft weiter an Bedeutung gewinnen wird.« Hofmann sieht hier die Industrie gefordert, neues Wissen aufzubauen, um mit diesen Herausforderungen umzugehen zu können«. Industrie 4.0 bezeichnet er als »Sammelbegriff von Maßnahmen, Methoden und Werkzeugen, etwa Design Thinking, Artificial Intelligence und Industrial IoT, die reif genug sind, um diese Herausforderungen zu bewältigen.« Hofmann pflichtet auch Wolfgang Leindecker bei: »Es geht darum, wie wir mit Normen und Standards die Kommunikation zwischen den Maschinen und Produktionszellen aufrechterhalten bzw. ausbauen können, und wie man Daten in gesicherter und geordneter Form zur Verfügung stellt. Pilotfabriken sind da ein ganz wichtiges Vehikel, um Knowhow aufzubauen und in die Industrie zu transferieren, wie man mit einem heterogenen Maschinenpark umgeht. Es wäre natürlich schön, eine homogene Fabrik von einem Hersteller zu betreiben, wo alle Maschinen einfach miteinander kommunizieren. Aber die Realität sieht einfach anders aus: 99 Prozent der Fabriken sind heterogen«, stellt Hofmann fest.
„Neben den technologischen Herausforderungen geht es aber zusätzlich darum, nun die User-Experience in diesen Veränderungsprozess zu inkludieren. Das Ziel des neuen ganzheitlichen Ansatzes von SAP Leonardo besteht darin, Unternehmen und in ihrer gesamten digitalen Innovationsstrategie zu unterstützen. Es besteht aus mehreren Ebenen, einer Methodenebene-, einer Technologie-Ebene, die u.a. Machine Learning, Analytik, Blockchain oder AI beinhaltet, und baut dann zusätzlich auf Knowhow und Erfahrungen auf, die wir aus den unterschiedlichen Branchen einbringen: d.h. wir haben bereits bestimmte im Markt erprobte Anwendungsfälle und Referenzen“, erklärt Christoph Kränkl. „Mit Design Thinking Workshops schaffen wir es mit unseren Kunden in vier Wochen bis zur Umsetzung eines Prototyps und in sechs bis acht Wochen zum functional Prototyp“, so Kränkls konkrete Zeitangaben dazu.
Digitaler Zwilling und Zukunft
„Das ist ja das, was wir derzeit unter Digital Twin, digitaler Zwilling, verstehen. Ich baue mir den digitalen Zwilling meiner Fabrik und verknüpfe mehrere Datenquellen. Und um nur ein Beispiel zu nennen: Bei einem heimischen großen Unternehmen der Prozessindustrie haben wir schon sehr früh, vor fünf Jahren, begonnen, den digitalen Zwilling der Fabrik zu machen – und dann auf Basis der gewonnenen Daten, Optimierungen vorzunehmen – ganz spezifisch für einzelne Produktionsbereiche“, erzählt Hofmann, „nur Datensammeln und irgendetwas schön visualisieren ist sicher zu wenig – wir wollen konkrete Aktivitäten auslösen, z.B. Produktionsneuplanung, Maschinen-Wartung, Logistik, Optimierung, aber auch z.B. Mitarbeiter Schulung.“
In der technischen Produktentwicklung gehören geometrische Beschreibung, Simulation und die Schaffung eines digitalen Abbilds auch im Betrieb schon lange zum Repertoire, „die Herausforderung liegt darin, auch für intelligente, vernetzte Produkte (sog. Cyber-Physische Systeme) in diese Richtung zu gehen – da bin ich ein bisschen vorsichtig mit dem Begriff digitaler Zwilling“, meint Univ.-Prof. Gerhard. „Aber wir müssen künftig in der Lage sein, dem Kunden eine verifizierte Aussage geben zu können, dass ein intelligentes System robust arbeitet. Beispiel Autonomes Fahren, da sind in jüngster Zeit auch einige unschöne Unfälle passiert: Ein Kunde will ganz genau wissen, was er kauft. Und in dem Moment, wo die Dinge immer intelligenter werden, wird es sehr schwierig, das Systemverhalten gegenüber dem Kunden für jeden erdenklichen Fall dokumentieren zu können, da geht es dann auch um ethische und rechtliche Fragestellungen“, stellt Gerhard fest.
Bei der Plattform Industrie 4.0 „geht es uns darum, gerade auch für heimische Klein- und Mittelbetriebe Vorarbeiten zu leisten, etwa Normen und Standards zu konsolidieren, oder Handlungsempfehlungen für Forschung und Qualifikationserfordernisse abzuleiten. Gerade in punkto Geschäftsmodell-Innovation werden wir noch viel mehr konkrete Use Cases zeigen, um das Verständnis zu schaffen wieviel eigentlich schon in der heimischen Industrie zum Thema i40 unternommen wird“, betont Christian Hofmann. Hierzu werden wir für die Mitglieder der Plattform mehrere use-case days dieses Jahr abhalten. „Die Anwendungsfälle gehen vermehrt in Richtung Outcome Based Businessmodelle – die Unternehmen sind sehr zurückhaltend, die Modelle, die sie heute schon haben, am Gesamtmarkt zu kommunizieren, derzeit sind häufig nur Pilotkunden in diese eingeweiht. Wir werden aber in naher Zukunft ECO-Systeme entlang einer Wertschöpfungskette sehen, die kooperative i40 Lösungen mit gemeinsamen Datenräumen entwickeln werden“, fügt Hofmann hinzu.
Für den Standort beurteilt Wolfgang Leindecker die Veränderungen optimistisch: „Ich glaube, wir befinden uns in unserer Region in einer wunderbaren Ausgangslage: die Automatisierung kommt größtenteils aus Mitteleuropa, die ganze Welt schaut auf das, was hier passiert. Die hier ansässigen Maschinenbauer dominieren den Weltmarkt. Entscheidend ist, dass wir den Sprung auf die nächste Generation nicht verpassen und dass wir unseren Technologie-Vorsprung jetzt zu unserem Vorteil nutzen.“
Be the first to comment