Bei Perusch-Paletten ist längst Realität, was für viele Unternehmen noch ein Traum ist: Die smarte Fabrik mit vollautomatisierter Fertigung und einem durchgängigen ERP-MES-System als Datendrehscheibe. [...]
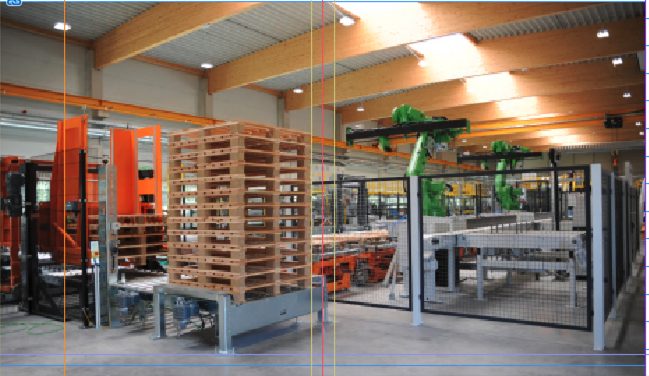
Durch die Realisierung des Mammutprojekts ist Perusch heute auf dem besten Weg zur Kostenführerschaft in einem Markt, der herausfordernder nicht sein könnte. So gilt es, eine riesige Variantenvielfalt bei kurzen Auftragsvorläufen zu beherrschen und einem kontinuierlich zunehmenden Preisdruck im globalen Wettbewerb standzuhalten.
Für einen Hersteller ist eine Palette weit mehr als ein paar Trag- und Deckbretter, zusammengehalten von ein paar Nägeln und Klammern. Denn um die Transportsicherheit von Waren auf den Paletten sicherzustellen, muss er neben offensichtlichen Eigenschaften wie das Format oder Kufenmaß weitere, vielfältige Parameter beachten. Dazu zählen z. B. Traglast, Folienüberstände, Deckelanforderungen oder Stapeleigenschaften. Selbst innerhalb bekannter Standards wie z. B. Nonstop-, Export- oder Papierpaletten ergeben sich hieraus theoretisch unendlich viele Konfigurationsmöglichkeiten. Kurzum: Fertigungsunternehmen wie die Perusch-Paletten GmbH müssen eine riesige Variantenvielfalt beherrschen.
Und nicht nur das. Denn zur großen Herausforderung wird die Variantenvielfalt vor allem in Kombination mit dem steigenden Kostendruck, den recht kurzen Vorlaufzeiten und Just-in-Sequence-Lieferungen an die Kunden. Beim österreichischen Familienunternehmen Perusch etwa hat ein typischer Kunde – vorrangig mittelständische Papier- und Kartonagenproduzenten – einen Palettenbedarf von über 100.000 Stück pro Jahr. Diese werden über mehrere LKW-Ladungen pro Tag ausgeliefert. Da ist höchste Präzision in allen Prozessen gefragt. Für Perusch hat in diesem Zusammenhang das Thema Automation immer weiter an Bedeutung gewonnen: „Mitte der 90er Jahre schafften wir die ersten automatisierten Maschinen an. Seit 2006 betreiben wir zwei weitgehend automatisierte Fertigungslinien“, erzählt Wolfgang Perusch, der gemeinsam mit seinem Bruder, Ernst Perusch, das Unternehmen inzwischen in dritter Generation führt und die Bereiche Technik und Produktion verantwortet.
Mit „Perusch-Paletten 4.0“ zur Kostenführerschaft
Zuletzt haben der steigende Digitalisierungsdruck sowie die voranschreitende Globalisierung den Druck weiter erhöht. Und die Perusch-Brüder wollen künftig weit mehr als nur standhalten: „Wir wollen Cost Leader bei der Produktion von Karton- und Papierverpackungspaletten werden und das bei gleichzeitig maximierter Flexibilität“, bringt es Wolfgang Perusch auf den Punkt. In Zahlen bedeutet das eine Erhöhung der Stückzahlen von zuletzt 900.000 auf 1,4 Millionen pro Jahr, und zwar mit dem Bestandsteam von 38 Mitarbeitern. Dieses Zielt ist nur erreichbar durch eine starke Reduzierung des Anteils manuell gefertigter Paletten, durch die Beschleunigung der Auftragsdurchlaufzeiten sowie eine optimale Verwertung der Ressource Holz. Hierfür wurde das aus Mitteln des Europäischen Fonds für regionale Entwicklung kofinanzierte Projekt „Perusch-Paletten 4.0“ und damit die größte Erweiterungsinvestition der Firmengeschichte ins Leben gerufen. Das Projekt zielte folglich auf die Modernisierung der gesamten Fertigung ab, mit einer maximalen Ausschöpfung der Digitalisierungsmöglichkeiten und einem höchstmöglichen Automatisierungsgrad. Dazu zählten der Bau einer neuen Produktionshalle mit einer Fläche von 1 .507 m² sowie die Einführung der ERP-MES-Suite PSIpenta der PSI Automotive & Industry GmbH als Datendrehscheibe der smarten Fabrik.
Tiefe Integration von Shopfloor, MES und ERP
Die neue Fertigung besteht aus drei tief integrierten Ebenen. Zur Shopfloor-Ebene zählen die neue Produktionsanlage mit einer Sägelinie und einer Stapelanlage mit zwei Industrierobotern, ein Intralogistiksystem sowie eine Industriefertigungslinie. Daran angedockt sind als zweite Ebene die MES-Module, die wiederum voll in das ERP-System integriert sind. Die dritte und höchste Ebene bildet das ERP-System inklusive angebundenem Kunden-Webportal. Das Portal liefert dem ERP-System eine CSV-Datei, in der alle Kunden die relevanten Auftragsdaten erfassen. Ab hier plant und steuert die Software den gesamten Auftragsdurchlauf im Zusammenspiel mit den verschiedenen Komponenten der Produktionslinie vollautomatisiert. Vom Eingang des Kundenauftrags über die Produktion bis zur Etikettierung und Auslieferung. So generiert PSIpenta zunächst automatisiert Kundenvorgänge, Fertigungsaufträge und Stücklisten und übermittelt durchschnittlich 270 kundenspezifische Parameter pro Kundenauftrag an den Shopfloor. „Hier kommt das Variantenmanagement der ERP-Lösung zum Tragen. Vereinfacht gesprochen verwaltet es die spezifischen Ausprägungen unserer standardisierten Palettentypen und generiert Angebote, Aufträge, Stücklisten und Arbeitspläne für die konfigurierten Muster, und zwar auch dann, wenn es einen Auftrag in dieser Form noch nie gegeben hat“, so Perusch. Dann übernimmt der Leitstand, der wiederum die Fertigungsaufträge für die Montage automatisiert und auf Basis der Termine und Rüstzeiten einplant. Die Zuschnittaufträge und internen Liefertermine übergibt er im Anschluss einem integrierten Algorithmus. Dieser dient der Planung der Zuschnittanlage, welche die Bretter für die Produktion aus Langware kappt. Im Sinne der Ressourcenoptimierung errechnet er die optimale Ausnutzung der Rohware (Verschnittoptimierung) und zwar ohne Konflikte hervorzurufen. Ein digitaler Zwilling überprüft das Ergebnis schließlich auf Machbarkeit. Die ermittelten Daten schleust das System im Anschluss über die Säge bzw. Stapelanlage in das interne Logistiksystem, so dass es die Ladungsträger in der korrekten Sequenz an die Fertigungslinie fördert.
Zentraler Datenhub schafft Planungssicherheit
Perusch hat geschafft, wovon viele noch träumen: eine automatisierte, smarte Fabrik. Dazu hat auch beigetragen, dass die Rechnung, ein ERP-MES-System als Datenhub zu installieren, voll aufgegangen ist. So minimiert das System zahlreiche Aufwände und sorgt durch die automatischen Rückmeldungen der verschiedenen Stationen für eine hohe Transparenz. Sie versetzt das Unternehmen in die Lage, jederzeit den Status eines Auftrags zu kennen, was wiederum ein hochflexibles Planen ermöglicht. Für hohe Effizienz in der Bedienung des Systems sorgt schließlich das PSI-Click-Design, mit dem Mitarbeiter ihre Benutzeroberflächen an individuelle Anforderungen oder Bedürfnisse anpassen können: „Ohne unsere Mitarbeiter wird und soll es auch künftig nicht gehen. Umso wichtiger ist die Bedienfreundlichkeit der Software. Weil sich die Masken in PSIpenta auf das Wesentliche bzw. Relevante stark vereinfachen lassen, entsteht letztlich auch eine viel höhere Effizienz beim Abarbeiten täglicher Aufgaben“, so Perusch. Und er ergänzt: „Besonders wichtig ist für uns, dass uns das ERP-MES-System auch künftig nicht einschränkt, etwa wenn es um die Erweiterung der Systemlandschaft geht.“ Der noch laufenden Implementierungsphase mit Tests wird sich in Kürze der Go-Live der Produktion anschließen. Ab diesem Zeitpunkt will Perusch den Fokus auf die Sammlung von Produktionsdaten legen, um die Anlagen weiter zu optimieren.
Für die Zukunft gut aufgestellt
Perusch-Paletten hat mit der größten Investition in der Firmengeschichte das Fundament für eine erfolgreiche Zukunft gelegt. Einen wesentlichen Anteil an der Realisierung dieses Traums hat das durchgängige ERP-MES-System. Denn mit seiner Funktionstiefe, Bedienerfreundlichkeit, Offenheit und Flexibilität bringt es alles mit, was die Smart Factory auf IT-Seite benötigt.
*Jens Reeder istLeiter der Division bei Industry PSI Automotive & Industry GmbH und Karsten Bruckschweiger ist Teamleiter bei Österreich bei PSI Automotive & Industry GmbH.
Be the first to comment