Die Verflechtung von Industrie und IT nimmt immer mehr an Bedeutung zu. Die Automatisierung der Produktionen generiert große Mengen an Daten, die zur Optimierung und Abstimmung vieler Prozesse genutzt werden können – und sollen! [...]
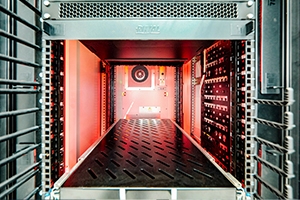
Der Nutzen der Digitalisierung einer Produktion beginnt bei der Energieeffizienz und führt über die optimale Ausnutzung einer Anlage bis zur anschließenden Lieferkette. Rittal hat daher die Gelegenheit genutzt und war auf der größten Automatisierungsmesse in Österreich mit einem Novum vertreten: einem Edge Data Center. Einem Rechenzentrum auf einer Industriemesse!
Das Thema IT-Infrastruktur stößt hier bei der produzierenden Industrie auf großes Interesse. Viele Produktionsleiter stehen in den Startlöchern. Sie wollen ihre Anlagen digitalisieren und optimieren, sie wissen nur oft nicht, wo und wie sie beginnen sollen. Dementsprechend groß ist der Bedarf an Informationen zu den Lösungen, die Rittal und ihre Schwesterfirma German Edge Cloud zu bieten haben.
Das richtige Data Center extra für die Produktion
Technische Voraussetzung für eine digitalisierte Fabrik ist ein Edge Data Center, welches die anfallenden Daten nahezu in Echtzeit aufnehmen und verarbeiten kann. Die fix fertigen Rittal Edge Bundles bestehen aus Rack, Power, Cooling, Monitoring und Security und decken den IT-Bedarf im Maßstab XS bis XXL ab – in Rittal Qualität und mit höchster Energieeffizienz bei der Kühlung.
Der nächste Schritt auf dem Weg zur professionellen Digitalisierung wird von den Kollegen der German Edge Cloud verständlich gemacht.
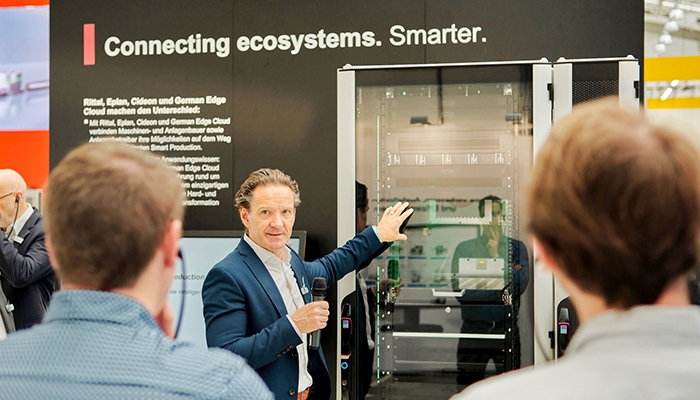
Marcus Welleschütz, Rittal Key Account Manager IT Infrastruktur, vor der Beispielkonfiguration eines Edge Data Centers auf der Messe SMART Automation 2023.
Im persönlichen Gespräch mit Bernd Kremer, COO der German Ede Cloud (GEC), wird schnell klar: Die Digitalisierung zieht eine notwendige Kommunikation aller am Prozess beteiligten Systeme nach sich. Schon ein zweiter Standort eines Unternehmens macht es erforderlich, dass Produktionssysteme digital aufeinander abgestimmt werden. Bestellprozesse und auch die anschließende Logistik sind weitere Systeme, die mit der Produktion kommunizieren sollten. Hier kann die GEC mit ihren modularen und skalierbaren Schnittstellen und Kommunikationslösungen, dem ONCITE Digital Production System DPS, helfen.
Die Daten sind da. Die Systeme müssen jetzt kommunizieren.
Bernd Kremer macht es deutlich: „Es wäre doch toll, wenn ich nicht nur über einen QR-Code an der Maschine sehe, wann und wie diese gebaut wurde, sondern wenn auch zu jeder Zeit bekannt wäre, wie viele Zyklen diese Maschine bereits durchlaufen hat, wann die nächste Wartung fällig ist, wie die Auftragslage ist und der Stand der logistischen Verfügbarkeit, die Temperatur oder die Qualität des erzeugten Produktes.“ Das ONCITE DPS kann dann aus diesen Daten heraus auch Kausalitäten erkennen und in weiterer Folge Prozesse und Produktionen optimieren. Diese Optimierung betrifft Energieeffizienz, Auslastung, Fehlergenauigkeit, Abnutzung oder Verfügbarkeiten.
Ist das schon KI in der Fabrik?
Ist die autark selbstlernende smarte factory damit schon in der Wirklichkeit angekommen? Bernd Kremer: „Noch arbeiten solche Systeme nicht vollständig selbstlernend, sondern mittels supervised learning. Das Validieren erfolgt weiterhin durch den Menschen. Es geht aber sicherlich in diese Richtung.“
Be the first to comment